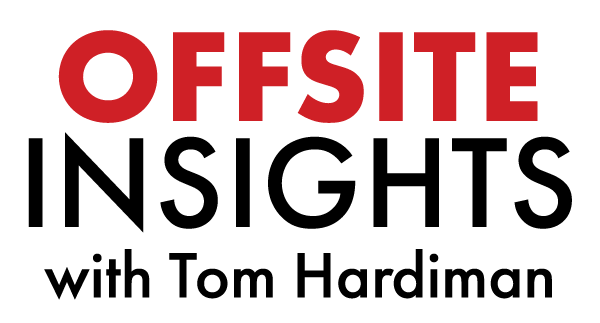
The State of Prefabrication in Canada
An interview with Craig Mitchell, Principal, BlackBox Offsite Solutions
Craig Mitchell joins Tom Hardiman to discuss his recent whitepaper, The State of Prefabrication in Canada, which drills down into each sector of offsite and prefabricated construction in Canada and abroad. He also discusses his current and recent offsite and modular projects in North America as well as the recent rise of affordable module housing projects in Canada.
Interview transcript
Tom Hardiman 00:00
I'd like to thank today's sponsor for offside insights. USG Structo-Crete brand structural panels are noncombustible mold moisture termite resistant, dimensionally stable panels for use in sub floor, roof deck or foundation wall assemblies. Structo-Crete brand structural panels meet the full criteria of ASTM E 136. For use and all types of noncombustible construction. Numerous one, two and three, our fire designs are available for modular, analyzed and conventionally constructed buildings to meet virtually any application. The panels are easily cut with standard framing tools, rapidly applied using mechanical fasteners and require no adhesive for installation. To learn more, visit www.usg.com/structocrete.
Welcome to another edition of Offsite Insights. I'm your host, Tom Hardiman, and I'm excited to have with me today, Mr. Craig Mitchell. Craig is the founder of a company called BlackBox Offsite Solutions. Craig, how are you doing today?
Craig Mitchell 01:10
I'm great, Tom, and it's good to see you again.
Tom Hardiman 01:13
Yeah, it's been a while. Maybe one of these days we'll connect in person, but for now, this is good. This is good. Keeping busy, I'd take it?
Craig Mitchell 01:23
Oh, yes. It seems as though with trade shortages, price escalations, seems that everyone is moving to offsite construction, or at least there's a greater interest in it I'll tell you that.
Tom Hardiman 01:37
That's good. Well, Craig, just for our viewers, tell us a little bit about yourself. Your background and a little bit about your company.
Craig Mitchell 01:44
Yeah, sure I can. So, I’m Craig Mitchell. I'm the principal and founder of BlackBox Offsite Solutions. We’re a consultancy service, providing unbiased advice to the offsite industry. Generally speaking, I work in panalization, modular and a little bit of mass timber. Generally, most of my career has been focused in the modular space for I would say 25 plus years now. Both with factories, as well as now in the last couple of years as a consultant, working around North America, providing some project management systems with project teams, and also a little bit of owners rep work, and also working with factories as well, in helping them move projects forward. I like the project type work where someone has a particular project that they are building. Typically, in the commercial space. I don't do single family modular or offsite homes. Generally speaking, most of it is commercial and that's the multistory stuff and other types of commercial projects. It's been good and there's so much interest right now, especially over the last few years, since COVID took hold that we've seen such price escalation and labor shortages and so forth in the construction industry that really the offsite industry as a whole has really grown as a lot more interest in in this sector.
Tom Hardiman 03:23
No doubt. So, you're based in the Vancouver area, but you do work all over the place, right?
Craig Mitchell 03:30
Correct. In my career, most of my work has been spent in sort of Western Canada, as well as up and down the West Coast of the US. Lately since COVID, everyone's moved online to Zoom and so forth here. Suddenly, that world became a lot smaller. So we've often found that it's really easy to connect now on the east coast or southern US. Right now, I'm working on projects in the Maritimes right now through relationships I have there.
Tom Hardiman 04:00
Excellent. I've read your bio and you've been in the construction industry for nearly 30 years. I've been the director of MBI for 18 years, we kind of go back a little bit. For those that don't know, Craig served on the MBI board of directors for several years, and was just an invaluable part of our leadership team during some really interesting growth time for the whole industry and associations. So, we appreciate your service there and I think he even won our volunteer of the year.
Craig Mitchell 04:32
Yes, I did. I'm on that list of very storied individuals. So, thank you for that.
Tom Hardiman 04:38
We always love it when people volunteer for us, especially with what you're doing. The main reason I wanted to talk to you today is you recently published a report called the State of Prefabrication in Canada, and you alluded to it earlier. It talks about mass timber panalisation and volumetric modular. Just a fantastic, comprehensive report, what prompted you to do that? Who was the client if you will? Tell us a little bit about that.
Craig Mitchell 05:07
Here in Vancouver, I have been working with a group called Forestry Innovation and Investment. They're the industry arm of the forest industry here in British Columbia, and I am on their first advisory committee as well. It's really a group of industry individuals that provide advice to the forest industry in terms of markets and sectors that they should be looking at, and doing market outreach. I got involved with them and I had a conversation with them. As we just talked about, there's been such growing interest in prefabrication, in the wood sector, really in North America. Look at changes in code with mass timber changing. Here in Canada it’s 12 stories, in the US it's 18 stories in the IBC. There's been such a growth in wood prefabrication, technology and interest that really, forestry innovation really didn't have a landscape piece here in Canada, in which to point to in terms of what was actually happening in prefabrication in Canada. Just through my connections, I'm also chair of the board here at the Vancouver regional construction Association here in Vancouver. Just knowing the construction industry and what's going on across Canada, they asked me, Would I look at doing a report, an in depth study of what was going on in Canada, and to help them assess where the market is at.
Really more than anything where we're in the evolution or is mass timber panalization that's open and closed wall panels. Then modular construction, really this landscape piece consisted of looking at academic research from around the world. What's going on in different environments and different countries. Also interviewing a lot of stakeholders and real leaders in any sort of sector. So, I conducted 40 Plus long form interviews with various individuals and thank you, Tom, you were part of that and provided your insight in terms of what was going on in North America for example, in modular construction. I would talk to academics and other people in the industry as well. So, it was a pretty comprehensive paper. It was done over four to five months, and it just got published this past year. A lot of the findings through the research could be applied to many countries in the world. It's not just particular to Canada, in terms of where some of this evolution is happening and the interest in prefabrication.
Tom Hardiman 07:53
Yeah, that's where I was going to say, it's a great report, regardless of where you are. I think often we're victims of the terminology issue where everything kind of gets lumped together as prefab or modular even. So, you do a great job of breaking out those different offsite solutions, if you will. So, we do have that report posted on our resources section if people want to check it out, they can get it there. So, any surprises in your research? It shows that you took four or five months to put this together.
Craig Mitchell 08:30
For sure. I would say there are a number of surprises. The evolution of what's going on in prefabrication right now is there's really a new set of drivers that we're seeing in the industry right now, versus ones that were maybe say 10, 15 years ago. Now, the McKinsey Report, everyone points to the McKinsey report about construction, it's lagging indicator on productivity. Back in 2017, when that report was published, that is heralded in this interest in construction technology and looking at how do we increase productivity. That's a different driver than what was present in the market, say 10 plus years ago.
Then we've got time performance drivers and cost performance as well in that, owners I think are finally waking up to the fact that the construction industry has a very poor track record when it comes to delivering projects on time at a fixed cost. I think they're realizing that and they're open to new ideas in terms of how to deliver projects more efficiently. Using technology plus looking at different forms of construction, I truly believe that we are in a different era now in that a lot of markets, it was one or two choices in terms of how you build a project. Is this a wood frame project or is this a concrete project? That was pretty much all that got tabled. Now, we have a lot more tools in the tool belt. I like to say that we have opportunities to do maybe a hybrid building, maybe concrete foundations, and maybe mass timber. Maybe we're using panalisation, or modular construction above grade. Now we're starting to mix the different forms of construction and we're being more open to different forms of construction.
Tom Hardiman 10:36
So great case study from PCL contractors in Canada and it was just that as a hybrid, it was a hospital, but they used prefabricated head walls, bathroom pods, it was just a great, truly a hybrid project. It was done on time and on budget.
Craig Mitchell 10:58
Yeah, exactly. I think that move toward offsite construction, we've long talked about it, but it's just that cost certainty. We've just gone through COVID here, where we've seen escalation in construction supply, materials and labor of 25 to 30%, all the way across North America. People are looking to how do I get cost certainty on projects? Obviously, prefabrication can deliver that, because a lot of those early decisions are made during the design development phase. You're not waiting for a building permit and then have to go in procurement, your materials, and total months might have passed going through that process. So, a lot of that is just more interested in looking at different forms of prefabrication. The, the other two areas and drivers that I think are really important, too, is with the trade shortage, too. We talked about quality of the finished product, at the end of the day, we do know that building inside a factory does provide all those benefits on quality assurance and so forth. I think one step further than that is that the construction industry right now, we're talking about trade shortages. It's more than that to we're actually talking about supervision shortages, and who's overseeing the work of the trades from a quality assurance standpoint? We're seeing site superintendents now on construction sites who are now attending to four or five different projects at one time and that's ridiculous. You need constant supervision on commercial projects and we're seeing companies are so short-staffed that they just don't have adequate safety supervision. That leads to poor quality of end product. I truly believe that, again, moving a lot of this quality assurance to a factory-controlled environment is to the benefit of everyone, the owners, as well as the contractors themselves.
Tom Hardiman 13:04
A good take on that. I think there's this perception that if a project goes modular, offsite or panalized, that there's less work for the site built contractor. I think we need to do a better job of educating everybody, that it could lead to a greater use of your time, more projects completed, higher profitability, if you can figure out the right balance between onsite and offsite.
Craig Mitchell 13:32
Yeah, you're absolutely right. I think there's always going to be the requirement for onsite presence and putting a modular project together or a panelized project together. Just that coordination piece is so critical to the success of those projects. You can address that supervision piece as well.
Tom Hardiman 13:53
I interrupted you.
Craig Mitchell 13:55
I was just going to touch on the last driver here is really just the sustainability side of things. Changes in building code and policy is really driving the interest in prefabrication. We're finding this on the mass timber side and the panalisation side. Mass timber, carbon sequestration, looking at obviously wood products and embodied carbon is front and foremost in everyone's mind. You're starting to see leads taken by the big companies, the Walmarts of the world, Google, Microsoft, Amazon are all starting to build head offices in mass timber because they want to showcase that they are green, sustainable companies. I think we're going to see a lot more of that. The change in the building code there has really driven the sustainability conversation and as we start getting into requirements on energy codes and so forth, you're going to start seeing the move toward more prefabrication. Some of these, no envelope systems are so complex that the regular site framer is going to have difficulty meeting the requirements on site. So, the only way to do that is to move it into a factory. That's what we're starting to see on the sustainability side.
Tom Hardiman 15:22
Well, I'm glad you mentioned that. You've been an advocate of sustainability for many years before it was even cool. In fact, you might have been one of the first people where I heard about Passivhaus design and might have been from your company back in the day. I'm glad you mentioned the sustainability piece, I think a lot of people assume that modular and panelized, and particularly mass timber is greener. Then it's hard to really kind of quantify that. We are starting to see that become more and more of a driver. I recently talked to the MBI board of directors, and they've got an RFP out now to provide some more tangible research that we can point to. In particular, I think our industry and offsite in general, does a great job of minimizing the amount of waste that goes to our landfills. It's just drives me crazy how much waste there is in construction, and it's all just going to the landfill. At some point, these landfills are going to be full. We can't keep doing this. So, moving to that factory setting, we've got some research that will take place in 2023 that I think will quantify that. Instead of us just saying it's common sense. Of course there's less waste, we want to be able to point to something and say, here's the research.
Craig Mitchell 16:50
You're absolutely right. We've talked in generalities for so long that offsite construction is greener, or it's better-quality assurance, but unfortunately the construction industry works on hard. Owners work on hard, tangible evidence. You might be able to say an offsite project can be delivered 50% faster, while it's 50% faster than what? Or what's my cost saving as a result of that? It's very difficult to point to those and until the industry starts to measure those, we're going to be in a difficult position to really get the growth that I think we really want to see in this industry.
Tom Hardiman 17:31
I think you're right. I think there's more than enough case studies out there to document the Marriott 's of the world and the hotel chain saying we're saving eight months on the schedule. We can point to a lot of case studies. The cost that's going to vary, you know, 1000 variables involved there, but that sustainability piece, we can really start breaking that down. I want to be a part of that quantifying what that benefit is a little better. So, I think that's going to be important going forward. You're right, that'll be a big driver.
Craig Mitchell 18:05
Some of the outcomes, I think some of the recommendations I made as a result of a lot of the interviews, I'll just touch on a few of them here. We're definitely seeing mass timber. There's great push both in Canada and the US have really adopted mass timber as a building form. I think the one area that's lacking is how do we start integrating panalisation into mass timber? My recommendation is really to look at it from a single industry, from a market development standpoint. Often mass timber just talks about the actual structural frame of the building, whereas panels make a natural add in for building envelopes and so forth. We can start using panalisation and I think from a market development standpoint, especially in wood frame construction, you can start using those combinations of offsite construction in that construction method.
The other one that I think is really important, we touched on it a little bit here just during this conversation, is really the development of best practice guides for each form of prefabrication. That's really from early engagement to turnover. There's been best practice guides done for various forms, and I would say they're not complete from the research I've seen. Often, individual companies have done their own best practice guides in many cases and I think that's somewhat self-serving, but the industry as a whole have not done a comprehensive best practice guide. One of the drawbacks and uptick to get adoption is how to use these prefabrication techniques. I think when people are evaluating whether it's mass timber or modular, there's not a single document, resource, unbiased that a lot of these owners can point to, in terms of executing a project. I'm talking from early engagement to handover of a project. There currently is not a comprehensive guide for any of those forms of prefabrication. I think the industry as a whole need to get together and really adopt a best practice.
Tom Hardiman 20:32
You're dead on there. I think one of the things we, the Modular Building Institute, started noticing three or four years ago, we were doing a good job of promoting the advantages of modular and offsite construction and then it got to okay, how do I do this? It's everything. It's the procurement method, it's the financing, it's the insurance, it's the contracts, it's scheduling, integrating the offsite, it's all of the above. We have been chipping away at that, but you're right, it's kind of siloed. We're working with attorneys and consensus docs on some template contracts. Then we're working with Fannie Mae and up in Canada Morgan Child. On the financing piece, how do we finance a modular project? It's different. All of those things come into play. Once we started digging into that, and thinking, well, no wonder owners don't just jump into this. It's different.
Craig Mitchell 21:36
It's different. It's a minefield in some ways. You need to be knowledgeable in all these different parts and the information is exactly as you said, it's siloed. In so many areas, we need to bring a lot of that information into a comprehensive guide of some sort. From early inception right through to the end of the project.
Tom Hardiman 21:59
We're trying, but there's a lot of parts and pieces to go down. If you can figure it all out, the advantages certainly are there. The time savings, the cash flow, the sustainability.
Craig Mitchell 22:16
I'll just touch on a couple of other items here and you just touched on it. There's contract language and procurement, public sector procurement practices that I think are really key to driving more adoption. We're seeing that especially in Canada with some of the initiatives that have been present here with social housing, toward the affordable housing. As you mentioned, CMHC has carried out a rapid housing initiative. Where I live, BC housing really has done a fantastic job of adopting offsite technology for some of their projects. What we're seeing is, and you mentioned consensus docs in the US, but here in Canada, we just have standard construction language contracts that get altered every single time you have to pick up an offsite project and it feels like recreating a wheel. I think the lawyers are getting rich off of just doing supplementals for every single project.
Tom Hardiman 23:21
It was the same here until we worked with the group that develops the template contracts and we need one for prefabrication. So, we do at least now have one template contract specific to our industry and a second one that's about to be published. So, kind of gets along the lines of we need more industry standards. When you said best practices, I was thinking standards. There's got to be a standard way to inspect these units and a standard way to contract, procure, finance all of the above.
Craig Mitchell 23:58
Yeah, you're absolutely right. Here in Canada, we've implemented a new CCDC, our Canadian construction document. We've implemented a specific IPD contract, which is great for that integrated project delivery, where you're bringing teams together and offsite construction definitely fits that mold, but if you're going to do a construction management or a design build contract, you definitely need to adjust the supplementals to take into account some of the nuances of offsite construction.
Tom Hardiman 24:42
It took us two years to come up with that one template contract and you can imagine we had attorneys, insurance professionals. We had a couple of contractors and modular guys on there, but it took two years because we just had to think through who has liability of the module when it leaves the factory? All these different little scenarios. It's a lot to take in, hopefully with people like you and with the resources we have here at MBI and the Offsite Construction Network, we can give some owners some tools that make this a little less burdensome for them to figure out.
Craig Mitchell 25:22
Yeah, definitely. Yeah, really there's just a couple other minor ones here, I'll just touch on as well. We need to change the public sector procurement model. This idea of going to design bid build, and we've just seen it during COVID here, that doesn't work for construction. It definitely doesn't work for prefabrication. Through escalation, you're going to spend six, eight months of designing, you go to bed, and all of a sudden that original project budget is so out of line you're going back to the drawing board. We need to have a more collaborative type of environment. Prefabrication works a lot better when all stakeholders are at the table. That's owners, architects, consultants, your modular erector, your manufacturer, your installation team, everyone should be at the table. That's how you mitigate risk and changing that procurement model in the public sector is a difficult animal because it's so ingrained, that we really need to break down silos and looking at different methods.
Tom Hardiman 26:32
We face different defense departments here in the States. The people that work on the projects they’re 30-year bureaucrats in these government agencies. They're not real keen on changing the entire procurement process because it's one they understand. Sure, the project is over budget and never on time, but it's not their money. It's taxpayer money.
Craig Mitchell 27:00
I'll give a perfect example. Here in Canada, we just touched on the rapid housing initiative, mass timber companies, panel companies and modular companies were all quick to jump on the Rapid Housing Initiative. One of the drivers of that initiative was that you had to have your affordable housing project done within 12 months. Half of the first tranche of this $1 billion that Canadian Mortgage and Housing issued, went to municipalities to address homelessness and affordability in their cities. Well, the problem with the procurement model was that it went to municipalities and they go through a typical process of hire the architect, we're going to get a design, it'll have to go to city council for approval, and then by the time it goes through city council, they'll get a contractor on board through an RFP. Then it will go through a building permit, guess what the 12 months is up at that point. So, I think the whole model on the public procurement side definitely needs to change and needs to be more aware of different methods of prefabrication, different contract models for procuring projects.
Tom Hardiman 28:21
I'm all for public officials, safeguarding and ensuring taxpayers are getting the best value and going through the process, but at least here in the States, they're not getting the best. It’s like nobody's looking at it. I think we can do better.
Craig Mitchell 28:40
Yeah, we can do better for sure. One of the one of the highlights that came out of the report was a certainty around that building permit process and development permit process. It seems to go into a black hole at City Hall and no one knows the timelines surrounding when those permits will be issued. That's to the detriment not only of the construction industry, but also prefabrication. In terms of if you had certainty around when projects were going to get released, to start on site, you could then have a lot of that pre work done ahead of time. Some of the advantages of prefabrication are lost as a result of slowdowns and red tape at a lot of these building departments. So, we need to streamline that. That's actually first and foremost.
Tom Hardiman 29:34
Excellent. Well, any other cool projects or initiatives you're working on these days? Are you just taking some time off after writing the big report?
Craig Mitchell 29:43
It's been busy for sure. I'm working with a fantastic group right now in the Maritimes and on the east coast of Canada right now. We're just finishing off a rapid housing, four story project there and it looks like there's some more interest in some more work there. That was really one of the first projects that was done in that neck of the woods, that multistory project. We put together a really fantastic team and really exceeded the owner's expectations in terms of delivering on the project. I think it's really piqued the interest of others in that area. So, there's definitely still interest on the west coast here. I think if you go all the way up and down the west coast, there's interest in the affordable housing issue, homelessness and so forth. I think that is an area that really is not going to go anywhere or go away anytime soon.
I'm involved right now in several projects on the west coast here in BC and in California right now, where they’re trying to solve some of these homeless issues using prefabrication. Again, it's got to be the right fit. That is one of the differences between Canada and the US I think. The way that publicly funded projects get developed in the US differs than in Canada. Canada, when we make the decision on a affordable housing project, the project gets funded in its entirety and you're off to the races. I found in the US that there's a several sort of tranches of funding that get released to build the project and sometimes you miss that window, especially when we see things like cost escalation and things like that happening in the marketplace. It's a little more of a difficult environment compared to Canada.
Tom Hardiman 31:47
Yeah, and it's a huge problem everywhere. We've had events in Sacramento, in Denver this year and the homeless issue is right there. It's in your face. It's a growing problem and I don't think it's just large urban areas. I think it's everywhere that has affordable housing challenges. So hopefully, we can help put a dent in that. I like to tell well, we're not going to solve the affordable housing crisis, we're not going to solve homelessness, but we can help put a dent in or play our part. I think we've got a lot more to offer as an industry.
Craig Mitchell 32:20
Yeah. I think one of the things that came out of the report, I would say is it’s not just a Canadian issue. It’s across really North America. Really the industry and government need to start working closer together. We find it's often too siloed and that the government has their own initiatives and their own agenda, but they're not talking to the construction industry and how to solve them. We need to do a far better job of that integration and discussing about how do we deliver something faster and more rapid? I would say we're on the right track here in Canada.
Tom Hardiman 32:59
Yeah, your government said let's go build housing, here's some money, and use modular. In a way you win.
Craig Mitchell 33:11
It was great. Although, it would have been great to have a bit of a market sounding in terms of capacity, timeframes and everything else.
Tom Hardiman 33:20
We were floored. I know we're running short on time, but we'd been working with CMHC for a few years prior and they were kind of standoffish to modular and prefab. Then they kind of start to embrace it and then they just throw a few billion dollars at it and said, Let's go.
Craig Mitchell 33:37
That's right. Wow, that's great.
Tom Hardiman 33:41
We got a long way to go here in the States with particularly our federal government. We're making some progress in a lot of states though, so that's exciting. So, we'll get there.
Well, Craig, thank you so much for talking to me today. A lot of good insight and I think we just barely scratched the surface. We could probably chat for a few hours over this. Maybe next time, we'll get together, have a beverage and pick up this conversation. Until then, our viewers will be checking this out and be sure to check out Craig's State of the Prefabrication in Canada. Like he says it likely applies everywhere. It's a great resource. We appreciate your time today, Craig, thanks for joining us.
Craig Mitchell 34:25
Thanks again, Tom. It's been fun.
Tom Hardiman 34:28
Thank you, Craig.
Don't Miss Our Upcoming Events!
Join the leading companies and professionals from across the offsite construction industry at each of this year's Offsite Construction Network events. With summits and expos taking place across North America in 2025, it's never been easier to connect with and learn from offsite construction manufacturers, designers, builders, and suppliers from the United States and Canada.
Subscribe today to get the latest updates on future events from the Offsite Construction Network.