Component Use in Offsite Construction
When thinking about a construction project, most people picture building new structures from the ground up, starting with the first shovel of earth. This picture is correct for traditional construction styles. However, offsite work is beginning to take precedence as the industry adopts more prefabricated techniques.
Defining Offsite Construction
Offsite construction is a broad term that encompasses everything that goes into a project that occurs somewhere other than the final site. It can include manufacturing, design, fabrication and even some stages of assembly. Each step doesn’t need to be done at the same location — it just needs to take place elsewhere.
People may also see terms like offsite manufacturing, production and fabrication used interchangeably.
Permanent Facilities vs. “Flying Factories”
Offsite construction sites come in two flavors — permanent facilities and temporary “flying factories.” Permanent facilities service all construction sites in a given area. Freight shipping can get expensive for projects at the edge of the service area, but it still ends up being a more cost-effective and time-saving option than traditional building techniques.
Flying factories are temporary facilities that provide components to a construction site before moving to the next location. This option can be more cost-effective for companies that operate in a broad area. They also have the added benefit of setting up close to or on a building site, reducing or eliminating transportation costs and emissions. It’s also possible to have these locations closer to the source of necessary raw material components to minimize transportation costs while streamlining the supply chain.
What Are Structural Building Components?
Structural building components refer to any part of a structure designed to carry a load or support weight. They can take the form of wall panels, roof and floor trusses, columns and pillars, foundations, plinths, and even door and window frames. In traditional construction, all these components are built and assembled onsite. Offsite construction allows some of these structural components to be manufactured elsewhere, saving time and money.
It is important to note that while some structural building components may be utilized in factory-built modular or mobile home construction, it is a completely separate classification from off-site construction.
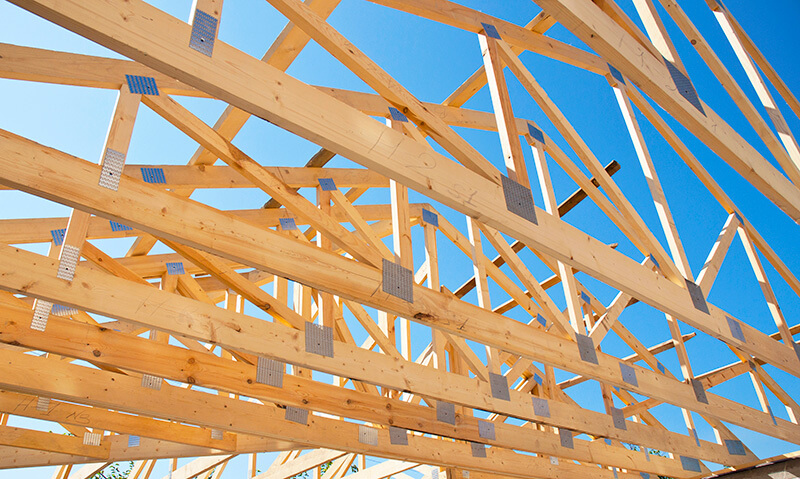
Roof trusses are the supports that create a roof’s frame. They can come in a variety of shapes and sizes depending on the design of the roof. In almost all cases, trusses are prefabricated in a factory and shipped to the construction site.
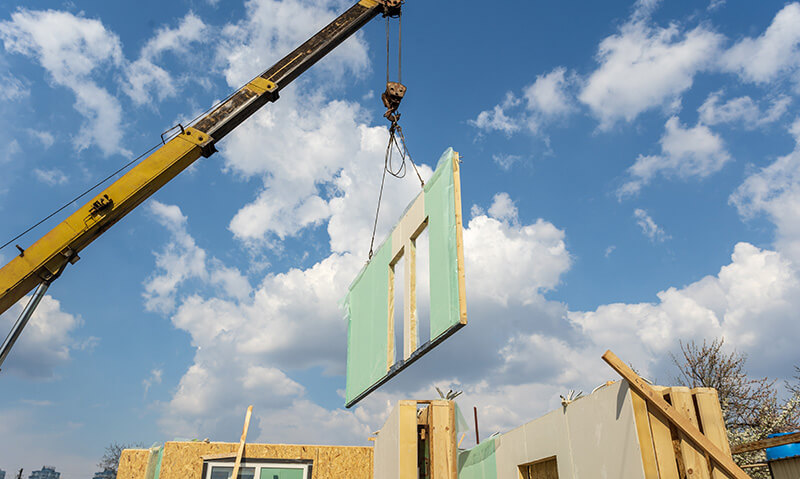
Wall panels are constructed in offsite building facilities and come in a variety of types. Structural insulated panels (SIPs), for example, are a high-performance building system for residential and light commercial construction. The panels consist of an insulating foam core sandwiched between two structural facings.
How Are Structural Components Manufactured in Offsite Construction?
The manufacturing steps for structural components necessary for offsite construction are similar to traditional methods. Instead of gathering the basic materials at the job site and building everything from scratch, companies can manufacture each structural component in a factory setting.
Offsite construction has numerous advantages over traditional methods. Onsite projects are often subjected to the whims of Mother Nature. Rain, extreme temperatures and more can interfere with building projects. Offsite manufacturing processes don’t have that problem. They can even continue operation during the cold winter months — often considered the off-season — so they can be ready to start assembling again as soon as the weather warms up.
Offsite construction also helps improve quality control. The steps are the same every time, unlike traditional methods. Much of the process could even be automated, eliminating the risk of human error. There’s no chance that cutting a piece of lumber an inch too short could throw off the entire process, leading to cost overruns or missed deadlines while someone fixes the problem.
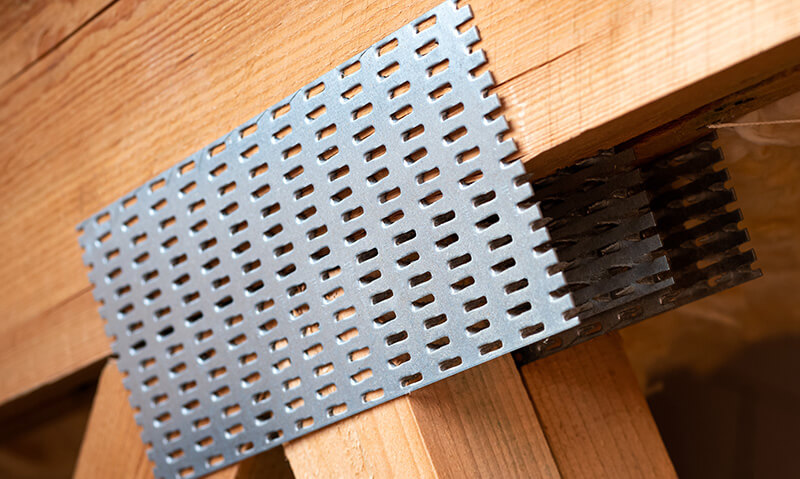
Invented in the 1950s, truss plates are light gauge metal plates used to connect prefabricated light frame wood trusses.
How Are Components Assembled?
People who have assembled a scale model may already be familiar with the basics of structural building component assembly. Items are delivered to the job site once they are manufactured. From there, framers work to install them alongside permanent bracing, building the overall structural system of the building. Then the rest of the construction crew can move in and install everything necessary to complete the project.
Installing structural building components often isn’t as easy as nailing a two-by-four. These massive prefabricated frameworks can be heavy and require additional equipment to move them into place. Cranes or forklifts can be invaluable for these installations, but the addition of machinery creates more safety concerns. Forklifts alone caused nearly 7,300 injuries and 78 deaths in 2020. It is essential to ensure that anyone operating these machines is well trained and experienced with this kind of work.
Benefits of Offsite Construction
There are several benefits of off-site construction over more traditional methods.
Studies show that off-site construction requires significantly less labor than the alternative. One study by the Steel Construction Institute found that implementing off-site construction could reduce the number of hands necessary to complete a building project by up to 75%. The case study looked at a four-story residential development but found that labor savings were similar on other large builds.
Off-site construction facilities also operate under a manufacturing rather than a construction model. Building professionals often need to collect various skills throughout their careers. Workers in a manufacturing plant only have to learn what’s necessary for their part of the assembly process. It’s still a specialized task, but the position requires less overall training time, making it easier to get employees in their jobs and working faster.
Traditional construction projects in residential areas can be extremely disruptive to those who already call that neighborhood home. Off-site construction, both for structural building components and modular projects, can help mitigate that disruption by reducing the time necessary to finish a job.
Off-site construction can even be beneficial for preventing job site theft. The loss of materials and equipment costs the industry between $300 million and $1 billion annually. Reducing the number of raw materials and equipment left on-site makes it more difficult for thieves to make off with anything of value. The reduced construction time also means there are not as many nights to worry about when the job site is left empty.
The Future of Structural Building Components
Structural building components are a small part of a growing trend of offsite construction, but it is something people will likely see more of in the coming years. The industry is shifting toward prefabricated techniques and off-site assembly to reduce costs and shrink its carbon footprint. It might not be long before all major building projects rely on off-site component manufacturing.
Don't Miss Our Upcoming Events!
Join the leading companies and professionals from across the offsite construction industry at each of this year's Offsite Construction Network events. With summits and expos taking place across North America in 2025, it's never been easier to connect with and learn from offsite construction manufacturers, designers, builders, and suppliers from the United States and Canada.
Subscribe today to get the latest updates on future events from the Offsite Construction Network.