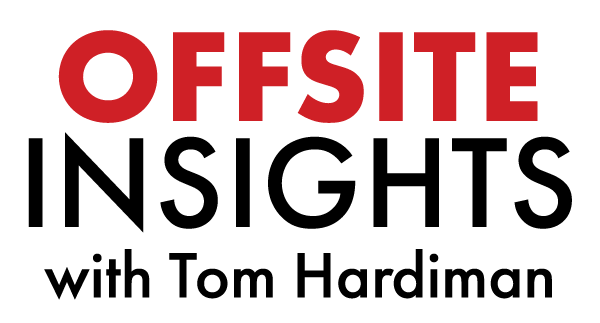
The Advantages of—and Advances in—Structural Insulated Panels (SIPs)
An interview with Jack Armstrong, executive director of the Structural Insulated Panels Association
Jack Armstrong, executive director of the Structural Insulated Panel Association, joins Tom Hardiman to talk about the state of the SIP industry and the advantages of SIP panels in residential and commercial construction.
Watch more interviews
See the complete collection of Offsite Insights here.
Interview transcript
Tom Hardiman
I'd like to thank today's sponsor for Offsite Insights, USG Structo-Crete Brand structural panels are noncombustible mold moisture termite resistant, dimensionally stable panels for use and sub floor, roof deck or foundation wall assemblies. Structo-Crete Brand structural panels meet the full criteria of ASTM E 136 for use in all types of noncombustible construction. Numerous one, two and three hour fire designs are available for modular panelized and conventionally constructed buildings to meet virtually any application. The panels are easily cut with standard framing tools, rapidly applied using mechanical fasteners and require no adhesive free installation. To learn more, visit www.usg.com/structocrete.
Hello and welcome to another edition of offsite insights, the show where we talk to industry leaders and newsmakers in the offsite construction space. I'm your host, Tom Hardiman and I'm excited today to be joined by Mr. Jack Armstrong, who is the Executive Director of the Structural Insulated Panel Association, also known as SIPA.
Jack, how are you today?
Jack Armstrong
I'm well. Thanks, Tom for this great opportunity to join your interview sessions here.
Tom Hardiman
Well, thank you for joining me. We'll, we'll jump right into it, but before we talk about SIPA and what SIPs are, why don't you take a minute and just tell us a little bit about who Jack Armstrong is. What's your background? How did you get into this offsite construction space?
Jack Armstrong
Sure. Well, you might say I was born way off site. I grew up on a cattle ranch in a little town in Hugo, Oklahoma. A town of about 4000 people outside of town to my family, 1000 acres and about 1000 cows. We later moved to Texas, got my chemical engineering degree started right out of college with a German chemical company on the Gulf Coast in the nylon business, nylon polymers. Then, over my career of 25 years with BASF, the chemical company, I worked in a lot of insulation products, raw material products, caulk, lids, adhesives, raw materials, things of that nature.
I spent some time down in South America, some time over in Europe, but really kind of the crux of it was maybe 2002 or 2003. I was in the experimental polystyrene business EPS foam business. I got involved with the Structural Insulated Panel Association as a supplier member for the resins that went into SIP panels. For those of you that maybe don't know what a SIP panel is, it's a foam core with a face or technology on the side, whether it's oriented strand board or whatever. People build with those for walls, floors and roofing.
Anyway, I was on the Marketing Committee, was on the board for a while. After 24 years leaving BASF, kind of start my own little sustainable construction marketing company, the board says, “Hey, Armstrong, what the heck are you going to do?” About that time that executive director was retiring. So, since 2013 I’ve been running the Structural Insulated Panel Association as the Executive Director. It's been a great ride so far, a lot of fun to be feet on the street with real products instead of just ingredients that go into it.
Tom Hardiman
Yeah, that's cool. You know, we talk to a lot of people, and we talk about their backgrounds. I talked to someone the other day that had a background in life sciences, human genomes and DNA. I'm like, did anyone ever go to college saying I want to be in the offsite construction industry? It's fascinating how we all kind of ended up in this space and given our varied background, it’s cool.
Well, tell us a little bit about SIPA. Who you guys are, what you do?
Jack Armstrong 04:11
Well, the organization has been around a little over 30 years. So, it was founded in 1990. It was really the collection of some likeminded people coming together that manufactured off site construction technologies. As you might imagine, back in the late 80s, early 90s, not many people were thinking about offsite construction technologies. It's really a manufacturing organization. We have about 25 SIP manufacturing board members that are manufacturers, probably another 25 or 30 supplier members, probably about 70 or so builder members, and maybe 50 or 60, designer, engineer, architect, team members, so just under 300. We really focus on educating the marketplace on what is a structural insulated panel.
Obviously, we have a website, SIPs.org, the continuing education credit classes and things like that, for architects. Really expanding the knowledge base, you might say, Tom, of what is the best SIP opportunity ethically to design and install in the in the marketplace, but more importantly common code reports, joint technical research, testing for seismic A, B, C, D, E, F. One hour fire ratings, two-hour fire ratings. So collectively, instead of the members all doing all these tests one at a time, we come together, and we do them jointly to try and kind of establish this baseline on the industry for who's a good company to buy from. Luckily, about 80-85% of the volume of all the structural insulated panels in North America, nominally about 18-20 million square feet are SIPA members.
So, we're excited to still be around and expanding in the industry.
Tom Hardiman
You're the trade association. You find the common interest in the industry and you're the advocate, the educator and the marketer.
Jack Armstrong
Exactly. So, trade associations come together and really give the best and the brightest light of what technology can do. You don't have to hear it necessarily from a specific company that has a vested interest in if you buy their product or not. We can be kind of a neutral broker of information and get people that trust, but also the industry cover when we're working with associations, like yourself, other associations, working in industry with the government.
We do a lot of Build America projects with the Department of Energy, and we have an allied association of all the other insulation industries where we do common advocacy in Washington DC about energy efficient tax credits for when people want to add more insulation to the roof or add more insulation to the walls or what that should really look like, or labor problems. We all have labor problems nowadays. So how to encourage whether it's immigration issues, or just training and vocational facilities, common industry issues that everybody has.
Tom Hardiman
Full slate of issues, there are no doubt. you touched on it in your intro, but tell us again, what is a structural insulated panel? I can kind of see in your logo and your background that gives you a good little visual of it. So that's a cool logo you've got there. Tell us a little bit about what is a structural insulated panel?
Jack Armstrong
Sure. Some people think a SIP panel is any panelized wall technology but the idea really of a SIP panel is there aren't individual dimensional lumber pieces or support structures within the ice cream sandwich or the Oreo cookie if you will. It’s a little bit before lunch so I'm thinking of food metaphors right now. So, you have that foam core of various thicknesses anywhere from say four-and-a-half-inch wall panels all the way up to 15–18-inch roofing panels. This foam core technology can be expandable polystyrene, it can be polyurethane foam, and typically because of the thicknesses, you don't often have like XPS extruded polystyrene foam because of just the thinner sheets that those come in. As a wall technology, roofing technology or even a flooring technology and in some parts of the country, a foundation technology, it provides rapid panelized walls and flooring that are anywhere depending on you know, when we did the RS means studies and things like that, you can shave off 30 to 50% of the building envelope framing time.
Depending on their factory produced product, designers will send their apartment diagrams, school diagrams or designs, the custom-built house, drawings and things like that. The SIP manufacturer interprets those into panels, that connectivity detail, the engineering for seismic and wind loading. I'm down in Fort Lauderdale, Florida, so we can design them all the way up to over 200 miles an hour and certainly out west for seismic D, E and F categories but in general, it's wooden construction. So, it's type five construction, just like regular wood construction that you can build with any other product you can build a structural plate of panels. The off-site gig is factory products that come precision cut loaded on a truck when you need them. They get delivered to the jobsite that go together with a lot of dimensional accuracy and you have a lot less waste.
Tom Hardiman
That's my next question. Some of the advantages: less waste, you mentioned; time savings on the framing schedule. That’s pretty significant.
Jack Armstrong
Nowadays, it's kind of funny. People always ask, how much time can you save? Well, it really depends on your style of building. So, we have 3-, 4-, and 5-story apartment projects that go up. Holiday Inn, Express Hotels, Marriott Courtyards, all the way down to tiny houses, and accessory dwelling units. So, the time element really varies. To really get the feel of it, you need to do more than one and many people try and do just one. Then they say, well, it was different. All in all, if you're a serious builder, probably working with three to five projects and after that you're kind of an expert, and you're kind of converted, you understand the efficiencies.
To be quite frank, Tom, the kind of sweet spot you might say, in the residential industry for building is somewhere between 18 homes a year to maybe 100 homes a year, people that are designing in that range. Certainly, custom builders use SIPs really well, but what we found is people that don't understand how to value their time. If you're a traditional builder, that's building three, five or six homes a year. Oftentimes, if you can frame a house in two weeks versus 30 days, you don't always charge that time as a billable expense. Carrying costs of being on a job site, three days or three weeks less somehow in the small list of the builder often doesn't roll out into really energy efficiency, economic advantage. We also try to focus specifically in the high-performance wall area. So, people that are building say in the residential space, high performance homes, zero energy homes, near zero energy homes, homes that usually have a HERS rating of less than 50. It used to be called a premium product and it was a caulk wall and roof system and it was more expensive.
Nowadays, with the advent of the 2012 codes, 2015 codes, 2018 codes, and certainly 2021 codes, continuous insulation requirements, you don't have to do that with a SIP product. It's really easy to get the air leakage rates way below the one or two air changes per hour.
So, all of those issues that now builders as they adopt in different states that the more modern codes, post 2012 International Energy Conservation Code, it's easy to kind of meet or surpass those mandates and those performance levels.
Tom Hardiman
Yeah, that's kind of what we're seeing is that each cycle of the code seems to step up a little bit on the energy performance and the requirements. That perhaps is steering more builders towards some of these offsite solutions. So, it's an excellent point, Jack. I thought it was mainly for residential products or projects, single family, but it sounds like hospitality, multifamily.
Jack Armstrong
Exactly. When we do our surveys of where SIPs are actually utilized, it's about 60% residential, 40% commercial. For example, in the state of Montana, the first LEED Platinum School University building just got built last year using SIPs. So, you can have 15, 20, 30,000 square feet facilities that are using a SIP envelope, sometimes they're all SIPs. Sometimes it may just be the SIP roofing solution, with insulated concrete walls, or sometimes it's the wall solution and a traditional roof. So, the versatility of a system like structural slate panels works well because you can marry it with hybrid designs. So, if you're doing a steel butler building, and you just need Curtain Wall technology to insulate the frame of the building. With SIPs, you can do that and not necessarily use the structural capability, or you can actually use the structural capability. So different people do different approaches.
The other thing that we have as well is what we call the one-sided SIP or retrofit insulated panel or rip panel. Nowadays in the renovation world, if you're going to maybe take the facade finish off of a structure and you want to add insulation in the walls or even on the roofing, you can add kind of a one-sided SIP and it provides kind of a nail base surface. So, you can choose two, three, five, eight inches of foam, and then you have your nailing surface on the top. Then you can revival side or reshingle or re stucco on the perimeter. Now that everyone's starting to think about renovation, carbon, global warming and trying to meet new municipal and state mandates with what is it our 70% of the buildings out there with no installation post or pre-1980? A solution like this is becoming more advantageous.
Tom Hardiman
Yeah. So, that's an excellent point. Are you I guess you're starting to see more and more applications for renovations versus new construction?
Jack Armstrong
Exactly. What we find a lot is, existing homes up in the Northeast, where you just didn't have insulation in the walls of these homes in Baltimore, Philadelphia and Boston, which were built in the 1800s, early 1900s. Certainly, prewar there's no installation in any of those walls. You can only employ a technology to, you might say wrap or blanket, the building from the outside, while the people are still living on the inside of it if you want to have a successful strategy to help people to kind of reduce their energy bills and footprint. I think the big thing with SIPs and like many of the other modular building technologies, speed of construction is a big one, right? Lower waste is certainly a big one and certainly the quality of the products coming together that were built in a factory and not in the elements like when you're building on site. For our particular technology as well, it's a lot about comfort.
So, it's quieter inside these buildings, they're less drafty because the air leakage rates are so low, there's a lot fewer seams that come together. So, if you're having to tape and seal different drawings, there's fewer of those. So, the framing factor on a technology like this is really low, it's in the three to 4% framing factor. Whereas when you have a two by four, or dimensional lumber every 16 or 24 inches, you have these high framing factors with all those thermal bridges. So, the comfort, peace, the thermal comfort, having the wall surfaces, and the roof surfaces not be cold, it just feels more comfortable. Now with COVID and indoor air quality, all that kind of is important to people now and they really understand now.
Tom Hardiman
Well, let me ask you this, as the director what's keeping you up at night? What's holding the industry from just exploding? What are the burning issues you've got?
Jack Armstrong
The older habits and resistance to change. You know, we've been doing it the same way for the last number of years. I was at the International Builder show this year in Orlando and because of COVID, fewer people went, but the folks that did go were like the younger crowd. So, you might not have had the old geezers and the guys like you and I that are over 50, but you have a lot of folks in their 20s 30s and 40s. They were completely open to new technologies and new ideas. When you say what keeps me up at night, certainly there's all the supply chain woes, but everyone has those issues. So, it's no different for the rest of us. It's really the fear of trying new things. Luckily, as we spoke about the codes, forcing people to have to build thicker walls or have to add extra layers for continuous insulation, these now are forcing the industry to have to come up with a new solution.
You know, you can do it in seven steps, or you can do it in three steps. If you could do it in three steps or fewer, why not do that? I think that it's the curse of not wanting to try something new, the inertia and the momentum that you have to overcome. Luckily, society is pushing us to those directions. I think we'll get there. NHB says 300,000 people are leaving the construction industry a year. So just retirement attrition and we're not able to replace those valued skilled labor artisans in the construction industry. It's time to embrace the modern world and build housing like we do automobiles.
Tom Hardiman
Yeah. I think that labor issues just continue to force contractors, no matter how reluctant they are, if you can't find workers, you're going to have to figure out a different way to build. I think what both of us are saying is to be open to some different ideas that maybe you haven't been open to in the past.
Jack Armstrong
It's a different business model. Having to get all your drawings reviewed and ready to go six weeks before you even pour your concrete slab is new to people in the old traditional building world. Maybe putting a 50% deposit on that stuff that's coming specifically to your job also is new. They do it for their specialty window packages, they do it with any other specialty package. Building envelope specialty assemblies are just like that. So, it's slowly happening, but it's never fast enough for the rest of them.
Tom Hardiman
You're right, it's that education process. It's just going out there, getting that message out there and that's what SIPA is doing and what Jack specifically is doing. I’m a big fan of trade associations, obviously, and I’ve said it, unabashedly, if you're generating revenue in the Structural Insulated Panel Association, you should support that association, you should support those efforts. I'm sure you've heard it Jack, I've heard it, I'm not a joiner. I don't like going to meetings, I don't care. If you're making money in that industry, you need to support the trade association that are representing it, because you guys are doing great things.
Jack Armstrong
Thank you. Tom, the really wide fence or circle that you've drawn around all things offsite with the Offsite Construction Expo and convening likeminded people that know how to plug and play different parts, I think that really helps to build the community. It's a trust factor, right? People just need to see, there's other people doing it besides me. I'm maybe not the early adopter or the innovator, but as I'm crossing that chasm and moving into the adoption curve for high penetration for these technologies, people are like okay, I'll give it a try.
Tom Hardiman
Yeah, maybe I'm not the only one out here thinking about this. So, what's on the agenda for SIPA? You got any upcoming events or exciting initiatives?
Jack Armstrong
I happen to sit on the board at the energy efficient building Alliance IBA, so many people know IBA is the high-performance training organization for builders. The IBA conference is at the end of September, out in Phoenix, Arizona, so we will be there and doing some training there. We're also working in conjunction with the National Association of Homebuilders building systems Council, so many of you may know the executive director, Devin Perry. They're finally in Atlanta after two years of absence due to COVID. Their summit is also towards the end of September and there will be an all day, day and a half training event for the different building systems. The Structural Insulated Panels Association will be there September 19.
Also, doing a half-day session on SIPs. So, if you're a builder or an interested person, in the technology of how it comes together, there's two great conferences coming up. The building systems Council conference as well as the IBA conference. I guess, follow our SIPA website, we have some great new, best practice documents that are out there and what we call the best training, the building education with SIPs training, the ESD. It’s a series of 10 videos where you can become a credentialed, registered builder and a master builder with SIPs. They're out there on YouTube and on our website, so you can just google how to build with SIPs. So, there's a lot of resources. Those would be two of the easiest ways to find us kind of as the year kind of gets past summer.
Tom Hardiman
I'll make it even easier. If you're watching this right now and you're on our offsite page, just click onto the Alliances tab. There's a whole section for SIPA and you can go right to their page from there. So yeah, check out all the resources here, including SIPA.
Well, Jack, it's been great talking to you, and I learned a lot today. Hopefully our listeners learned a little bit too. I learned that we're both old geezers, apparently.
Jack Armstrong
I never thought I'd be old enough to say that.
Tom Hardiman
Well, I do appreciate having you here. I do want to give a shout out to our sponsor for these Offsite Insights: USG. Thanks to them for sponsoring these series of interviews and with that, Jack, I'm going to cut you loose and tell everyone to stay tuned for the next episode of Offsite Insights. Check out our website, check out SIPA’s website and appreciate you being here today.
Jack Armstrong
Aloha until next time.
Tom Hardiman
Thank you, Jack.
Jack Armstrong
You’re welcome. My pleasure.
Don't Miss Our Upcoming Events!
Join the leading companies and professionals from across the offsite construction industry at each of this year's Offsite Construction Network events. With summits and expos taking place across North America in 2025, it's never been easier to connect with and learn from offsite construction manufacturers, designers, builders, and suppliers from the United States and Canada.
Subscribe today to get the latest updates on future events from the Offsite Construction Network.