Modularization Precedes Digitlization In Offsite Housing Delivery
Ivan Rupnik, Ryan E. Smith, Tyler Schmetterer
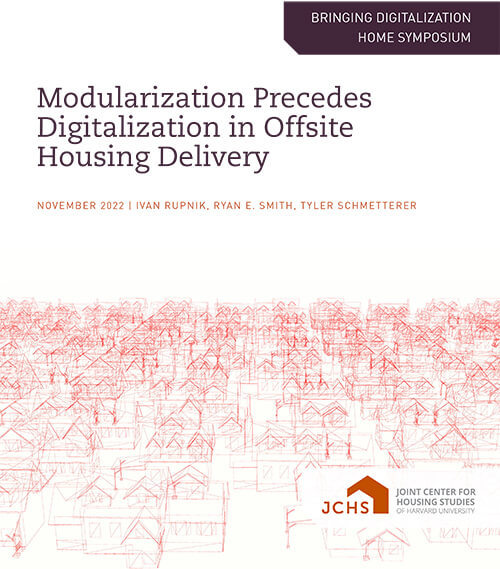
For much of the 20th century, architects, builders, developers, economists, and policymakers have pursued the dream of industrializing the construction industry to achieve quality, speed, and affordability in the housing sector. In the post-World War II era, US builders focused on single-family production housing and increased productivity and affordability through industrialized onsite wood-based construction. However, since 1968, manual labor has been favored over digitalization and automation, leading to declining construction labor productivity and rising housing costs. Despite the availability of digital tools such as Computer-Aided Design and Drafting (CADD), Computer-Aided Design and Computer-Aided Manufacturing (CAD/CAM) and Building Information Modeling (BIM), and regulatory frameworks, the construction industry has not seen the productivity gains that other industries have experienced through technology adoption.
Report Summary
The McKinsey Global Institute posits a two-pronged strategy to address the issue of stagnant and declining construction productivity. The first part of the strategy involves initiatives to "reshape regulation, rewire contracts, rethink design, improve procurement and supply chain, improve onsite execution, infuse technology and innovation and reskill workers" which could potentially increase sector productivity by 50-60%. The second part involves a shift to "manufacturing style production systems" or industrialized offsite construction, which could result in a 5-10 times increase in productivity. However, many players in the offsite construction market have jumped straight to digitalization and robotics without addressing the other changes to process and manufacturing principles. This has contributed to offsite construction failures and reinforced cultural hesitancy to evolve towards a manufacturing-oriented production process.
MOD X has developed a conceptual model that considers digitalization and technology within three frames: the contextual frame (i.e. market, material, labor, regulations, and culture), the business platform frame (value creation, supply chain, and integration), and the product platform frame (modularization, product platforms, assemblies, and continual improvement). Investments in digitalization and technology must consider these contextual frames to maximize the potential for affordability and accessibility in housing. The product platform frame is the closest to digitalization and technology and can have the greatest impact on capital investment, but it is also the least understood in the US context.
This essay will examine two key concepts in offsite construction - the product platform and the process of modularization - and how they have been implemented by international companies, Sekisui Chemical in Japan and Lindbäcks Bygg AG in Sweden. These concepts and case studies will be used to evaluate and progress the development of US offsite construction of housing. By understanding these principles, the US construction industry can realize the potential for increased productivity, quality, and affordability in housing.
Don't Miss Our Upcoming Events!
Join the leading companies and professionals from across the offsite construction industry at each of this year's Offsite Construction Network events. With summits and expos taking place across North America in 2025, it's never been easier to connect with and learn from offsite construction manufacturers, designers, builders, and suppliers from the United States and Canada.
Subscribe today to get the latest updates on future events from the Offsite Construction Network.