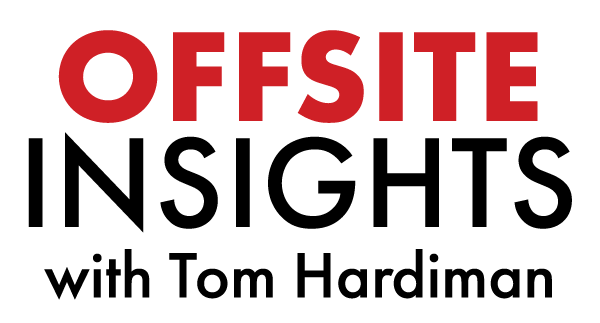
How House of Design is Evolving Offsite Construction
An interview with Shane Dittrich, Co-Founder of House of Design
Shane Dittrich joins Tom Hardiman to discuss how factory automation can change the offsite construction industry. Shane also discusses his involvement in Autovol and how House of Design worked collaboratively with different companies to create what Autovol is today.
Interview transcript
Tom Hardiman 00:00
I'd like to thank today's sponsor for Offsite Insights. USG Structo-Crete brand structural panels are noncombustible mold moisture termite resistant, dimensionally stable panels for use and sub floor, roof deck or foundation wall assemblies. Structo-Crete brand structural panels meet the full criteria of ASTM E 136. For use and all types of noncombustible construction. Numerous one, two and three our fire designs are available for modular panelized and conventionally constructed buildings to meet virtually any application. The panels are easily cut with standard framing tools rapidly applied using mechanical fasteners and require no adhesive free installation. To learn more, visit www.usg.com/structocrete.
Hello, and welcome to another edition of Offsite Insights. I'm your host, Tom Hardiman, and my guest today is Mr. Shane Dittrich, from House of Design Robotic Solutions in Nampa. Idaho. Is that correct? Shane?
Shane Dittrich 01:11
That's it. Yes, it is.
Tom Hardiman 01:13
Well, how are you doing today?
Shane Dittrich 01:14
I'm doing great. Doing good.
Tom Hardiman 01:17
Well, thanks for thanks for taking some time out and being a guest on the show. I think we've got a really interesting topic today and I want to go ahead and just jump right in. Why don't you start by giving us a little bit about your background, who you are and kind of how you got to where you are?
Shane Dittrich 01:32
Yeah, for sure. I grew up in Colorado, with just a working-class family, and went to school for airframe and powerplant mechanic. Out of high school, and then I went to college at Colorado School of Mines, got my engineering degree. It's probably a little bit different for your audience, but automation has its own industry. It is an industry where you have system integrators and system integrators are people that companies go out and they look at processes, they look at how they can automate them with hard fixed automation, robotics, those type of things. So, I worked for a couple of different system integrators. In 2012, my wife and I, and two other business partners decided to start our own system integration company. So that's kind of where House of Design came about. In 2012, we started the company and started it with just a few people, and we kind of wanted to keep it a small little company and that changed a lot.
Tom Hardiman 02:46
Okay, so House of Design and Robotic Solutions. Who are you guys? What do you do? Give me the elevator pitch here.
Shane Dittrich 02:56
We started out as a typical system integration company. So we would go and we'd look at any type of manufacturing process to see how we might be able to automate that process. We did a lot of medical device, a lot of general assembly type of applications but in 2018, a company that probably most of your audience knows Katerra came to us. We worked on a roof truss system, a floor truss system, and a plumbing stack system for Katerra. I think from our perspective, Katerra was one of the companies that embraced automation, and they tried to do a lot with it. It was a pretty hard set of projects that we took on there. Also in 2018, Rick Murdock, who you had on here a couple of weeks ago, great visionary in the industry, and had a huge vision to be able to come up and to automate a modular manufacturing facility. He came to us, and we worked together to be able to produce Autovol. We can talk about that if you'd like.
Tom Hardiman 04:20
So that's kind of where I was leading. I was unaware that you did work with Katerra and that’s such a huge company. A lot of people, off on a little tangent here, consider Katerra just this huge failure. I saw it as a way that, yes the company did fail, but it really moved the industry and maybe the construction industry as a whole not just our industry, moved us forward a big leap. Show people what is possible in the construction industry.
Shane Dittrich 04:58
I think that's my take on it. We did a roof truss system for them, trying to automate it completely, and we learned so much about your guys’ industry. So, automation likes things nice and consistent. We like things predictable, and we like to be able to repeat things. You look at a roof truss and you go, it's wood, not consistent bow twist, crook, Wayne knots, cracks, whatever comes with wood. A roof truss is completely different every single time. You don't get very much consistency with them. So, tackling those complex projects, in an open floor truss, same type of thing. Coming out of Katerra, we were in a position to where we actually had as products, and we sell right now to lots of customers out there, with roof trusses, and floor trusses. In automation, it started out as kind of this hard fixed automation. Actuators and very mechanical systems. It kind of moved into what we call flexible automation, which is robotics.
Robotics are there and we can program them to do very specific tasks, to be able to pick and place or do something very repetitive. What we dove into in these processes and these projects, is dynamic. That’s a term that we kind of use a lot now is dynamic. What's coming at us is we don't know; we don't know what the next roof truss looks like. It can be a custom home to where the roof trusses are completely different. So being able to have that component, which has a huge amount of software on the front-end side of it, as you can imagine. After Katerra, during the same time as Katerra, we went through and we worked with Rick, Curtis, and Merrick at Autovol to be able to come up with a way to be able to automate modular manufacturing. There's another company Wix Force Technology, they were a big part of it as well and Caleb Root for the Pacific companies was a big part of it also. A lot of people came together for Autovol, and it's been really good.
Tom Hardiman 07:38
Yeah, I was going to ask about that. So, I know you guys were involved in helping set up Autovol. I imagine Rick and Curtis didn't just go out and buy some robots, turn them on and started making houses. You mentioned the software on the front end, what was your role in that? What all is involved in starting what is the most automated modular factory in the country?
Shane Dittrich 08:03
Hands down. We were and are the automation supplier for Autovol. We did all of the robotics, which includes the software development for the robotics, and how to get the data from your guises’ world of sort of software environment, but how to make that and get that into the robotics language. So, we took on a lot of that. Autovol greatly helped and Prefab Logic, Curtis, they've done a ton of work on that as well, but we were the automation supplier. When you look through Autovol, we have every robot, every mechanical fixture, triad, they helped us with the convenience through Autovol, but it was a lot of companies coming together. As far as all the robotics, every robot doing any of the motion, any of that stuff, House of Design did all of that. So, all the fabrication, the integration, the testing, the programming, the development, all that stuff, that was that was House of Design, so very proud.
Tom Hardiman 09:21
You should be. Rick tells me all the robots have names. Did you help in naming the robots too, or no?
Shane Dittrich 09:27
Well, I think that's another question there that everybody has is robots are going to take our jobs and that sort of thing. I've lived with that my whole career inside of robotics and it just isn't true. Robots have helped elevate a lot of different industries, to be more affordable. I mean, we're talking about offsite construction. That's a hard job, construction in general is a hard job. I think Merrick did a really good job, how she did it was they had their employees’ kids name robots, I think is super creative. Autovol has a very, very good culture. I think that Rick has really driven that, and I think that's really good. Naming the robots isn't typically something a robotic system integrator would do. I think it was a fun little project that they had for the families that worked there.
Tom Hardiman 10:43
Absolutely. So, pretty limited experience with the modular industry when you started with Autovol, what kind of challenges did you run into?
Shane Dittrich 10:56
Oh, my gosh. There are so many challenges. I think that as an industry in the whole on automating offsite construction, there's a lot of opportunities out there and people are trying to do it. I encourage that. There's a lot of things to do, but there's nothing like having the hard knocks of actually doing it and we have those hard knocks. Understanding that a bunk of lumber coming in today and sitting on the plant floor could be grade one lumber, but with humidity and everything else, lumber changes. Wood is not a stable input into a system. So being able to work with Autovol, and being able to figure out those challenges has been really good, but those are hard knocks. Think about the number of fasteners that go into screwing down a sheet on a 74-foot-long wall. Statistically, if you're missing two or three screws, or two or three screws don't go in very well, as it goes through automation, you have to deal with that. Those were hard knocks and still challenges out there and stuff.
Tom Hardiman 12:16
I asked Rick this question, I'd be interested to get your take. You're probably familiar with other modular factories. You're right, we're kind of not quite construction, not quite manufacturing, we're kind of this in between. I'm sure you've heard from others about how robotics and automation cost too much. We like the way we do it. We've been doing it this way for 30 years. It works. Why mess with it? I'm sure you've heard that. What do you say to people that just kind of brush aside robotics and automation? Like, it didn't work for Katerra, it’s not going to work for anybody.
Shane Dittrich 13:00
Yeah, I'm sure that the first people that saw Henry Ford’s Model T, brushed it aside and said, this is never going to take. These horse drawn carriages is what are going to use forever and why would we do it? Look at those people like that, we all have our concerns. We all have our calculations on how we do our return on investment, and all that stuff. All that plays into it, but looking at how we did it at Autovol. I think Rick touched on it a little bit and I'll use names, maybe not of the employees there just because I want to be respectful of them, but a lady that is working on the infeed of the sub element station, she's been there since day one. She runs the complete sub element station and she owns it, she knows that thing inside and out. It’s a woman in the workforce that is doing offsite construction work, and she loves it. We had two other females running the sheeting station and younger people coming into Autovol to be able to run these things because they're not picking up a nail gun and shooting nails into wood. They're running a robotic system, they're excited about it and they like it. So as a job retention tool, they're not lifting four by eight sheets of chip and OSB. It's not back breaking work. Like how do we put those things into an ROI calculator?
Tom Hardiman 14:51
I think you've nailed it. There are a couple of things. The automation is attracting a different, maybe even younger audience to the construction industry. We have massive labor problems, as you know, but there's not a lot of young people entering trade school learning how to be a carpenter and a plumber. But they may be interested in learning how to operate a robotic piece of equipment. As a safety part, you're not just wearing people out day in and day out and by the time they're 50, they're just bad back, bad knees. They're done.
Shane Dittrich 15:32
Have you ever seen a roof truss being made on a manual table? It is back breaking work. They are bent over all day long, they are hammering nail plates into members. It is a tough job. And we expect to have those people have a career out of that job. Our roof truss system, we take the heavy lifting out. So, here's one thing that I would like to say just as somebody who knows automation pretty well, is people like to think that there's a term out there called lights out manufacturing. That is not where we're at in today's world. Lights out manufacturing is not, is not there. In some industries, it is but not offsite construction, I can tell you that. Use people where people are valuable. Where they add value to the process, help add quality into it. That's where on a roof truss system, we still use humans in that capacity and it's very useful. In order to automate it completely, we learned through Katerra, that that was a really hard job to automate it 100%. So what we said is, hey, use a couple of people where people add value and I think we did that in Autovol as well.
Tom Hardiman 17:05
I think, if I remember correctly talking to Rick, I think they are probably the most automated modular factory in the country. I think he said, they're really only automating about 20% of the work right now, they're hoping to ramp that up, but I would have thought that would have been much higher.
Shane Dittrich 17:26
I don't know those numbers. Rick would definitely be the expert in that, but what we automated at Autovol, is we automatically build sub elements, so window and door openings, that's all robotic. We do complete window and door openings that then get put into a wall as we extrude a wall. So we extrude walls, we frame them, we do all the framing to them, then it gets automatically conveyed into a sheathing station where we put adhesive, first layer down, which could be GIMP or OSB and then it goes to a second layer to where we put another layer of gimp on if we need it. We cut out all the openings automatically using robotics and then the wall gets transferred into the MEP station, like that's done, we've done that, and that is running every day.
I think we made like, 26 miles worth of walls last year, something like that. Then the floor ceiling line is the same thing. We automatically frame a floor and a ceiling and it goes down into a sheathing station where we're putting the sheeting down on the floor. We're working right now to get the ceiling up and running. So yeah, I mean if you just look at that piece of it at the end of it in a modular facility, what you're getting from the robotics line is you're getting a floor ceiling and all the walls for that box, and it's gone through a complete automated solution there. Then there's just a ton of work and Rick, and out of all they're the experts having the rest of the assembly process together. There are opportunities there. Of course, like, we're just going to keep automating this as we keep going.
Tom Hardiman 19:24
That's what I was going to ask you. I think MBI has about the trade association has about 100 or so modular manufacturers in North America. Very few of them are automated. If you were talking to a skeptical manufacturer, is this something they can dip their toe into, like what is the one thing everybody should be considering automating in their factories?
Shane Dittrich 19:54
Yeah, it's a great question. I think Rick mentioned the framing. Framing is just solid as rock. I mean, it just runs and runs and runs. I think our framing station had an idle time of like 30% last year. I mean you can just frame all day long. A lot of nuances in framing, though that you still have to consider, how it affects the wall down at the end, but framing is a good one. The one that I like and it's a hard process, but the sheeting, it's just because it's backbreaking. Putting sheets down onto a wall and doing that all day long. That's the part that's backbreaking. So, we have solutions for all of those things and we're actively developing standardized modular plants and that sort of thing. I tell people look at the framing side, I think that's a really good one, but don't be naive to it.
The cautionary thing that I'll throw out whether Rick would say it or not, I think we were all naive going into Autovol. We've learned a lot, but it was hard. The software aspect of it was a lot more than what I would have expected it to be, but it became a great tool for us. In the beginning, we were going to build standard boxes. Okay, right. Automation. We love standard. Boy, Tom, I call it the snowflake factory because I don't know if we built a standard wall, I mean I'm sure we have Curtis could tell you, I don't know the statistics. Every project that comes through different jurisdictions, different requirements, whether it's the bottom box on a multi-story building or the top box, it all looks different.
Tom Hardiman 22:08
We've talked about that so much in our industry. Everyone's building custom one-off projects, every time. It’s not real conducive to manufacturing.
Shane Dittrich 22:18
No. Build a box and let the architects have the outside to feed. That's what I've always said. Just build a standard box and let the architects have the outside of it and make it look different. I don't know.
Tom Hardiman 22:32
But that's the challenge. When you said you struggle, even just roof trusses, you would think if there's anything that could be standardized, a roof truss.
Shane Dittrich 22:43
Oh, my gosh, yeah and it's not. I mean, the complexity that we see come through our lines on roof trusses is insane. It's amazing.
Tom Hardiman 22:56
That’s a shocker. So, what are you guys working on now? What's new and exciting with House of Design?
Shane Dittrich 23:02
Oh, we're definitely working super hard on our roof trusses and floor truss systems. We definitely think that we have a great product on those, got a lot of good companies out there that are using them. We also see the modular manufacturing facilities being a huge opportunity and we're looking at trying to do more of those type of facilities, being able to help people out and encourage people to reach out to us if they have interest in that. Like you said, I have to believe if not in the world, at least in the in the US we're the only ones that have done a complete factory and that's a large part due to Rick's vision of being able to automate it and I give him full credit for that. But House of Design did do that automation in there, and boy, we're super proud of that.
Tom Hardiman 23:56
Yeah, that kind of leads into my next question. I guess it's one thing to start and build a factory kind of from scratch around the automation, but what about existing factories? Are you able to go in and say, let's take a look at this process and see what we can automate?
Shane Dittrich 24:15
Oh, absolutely. So, we have a standard product line of what we did at Autovol. The framing station sheathing station, the floor ceiling line, but we also have what we call the panel light. One, just a framing station that just does wall panels that’s super compact. It would fit into most manufacturing facilities and would be able to be used to dip their toe in automation, because that's a big thing. You got to understand the shift in mentality of going to automation. It's been amazing to see how the workforce sees a piece of automation come in, and how they react to it. Some people embrace it, and some people are scared to death of it. So, most companies should probably start out with just small pieces of automation and being able to do that. I think wall panels are really good, roof and floor trusses, just even some simple sheathing stations would be good.
Tom Hardiman 25:26
That's interesting. There are some parallels there. We often say if we could just get traditional contractors to shift their mindset a little bit to offsite construction, just give them that pause that moment to think about it, we can win them over. Even within our industry our own manufacturers are really kind of clinging to their history and their status quo. You start talking about automation and it's like, no, no, no, no, I don't want that. It's like, that's exactly what we want the construction industry to do, but we're reluctant to do it ourselves.
Shane Dittrich 25:58
It's so funny in your industry and the construction industry in general. Everybody thinks that they do it the best. That their way is the best and that everybody else is doing it wrong. That's just kind of what I've seen and I think you're doing a great job on trying to bring people together to be able to say, let's put our heads together and figure this thing out.
Tom Hardiman 26:24
Yeah. Like we've said, for years the modular industry and more little more broadly offsite, panelized, whatever you want to include in there, we're not really competing with each other anymore. It's these projects that are hybrid. We're working with site-built contractors, we're all trying to build what needs to be built, which is a lot of stuff with less labor. So, we've got to figure out how to do this. I don't think it's a competitive thing. I think there's plenty enough to build out there.
Shane Dittrich 27:01
But you're also saying we're trying to do it with less labor. The last two years, you're just trying to get labor. I mean, that's been the biggest problem right now and delays in construction projects because there is just no labor. I can tell you automation takes care of some of that, some of those heartaches.
Tom Hardiman 27:22
And attracting a different pool of labor. I don't think anybody thinks the labor issue is going to get better in the next five years, it's going to get worse. I'm hoping that if people are listening, that you've been able to kind of walk them off the ledge from oh, my gosh. I've heard webinars out there automate or die. It's like, you got to do this or you're going to be bankrupt. I don't know that it's that dire just yet. I do think there's a whole lot of room in the offsite construction sector for more automation, a whole lot more.
Shane Dittrich 28:06
I agree with that, and you don't have to go full automation like Autovol did. There is a step function change that you can have just by doing certain processes.
Tom Hardiman 28:19
I'm guessing people could reach out to you if they had some questions.
Shane Dittrich 28:22
For sure reach out to me, House of Design. We're anxiously going after things. The company now has some private equity, folks that have joined us, and it has been an amazing journey through it. So, I just hope that people can understand there's people out there that can help you and that have done it. We’ve just done it. I can tell you, and I'm sure Rick would also say like, there's been a lot of hard knocks that we've had to figure out and it's been difficult, and it's been challenging. Once you get to a stage to where they're at, I mean, they're producing.
Tom Hardiman 29:11
I'm very glad you're in this industry, in this space. Maybe you can help some others on their journey towards automation. Shane, I really appreciate you being here with us today. Do you have any parting thoughts for our audience?
Shane Dittrich 29:27
No. Thank you for having me and if there's any questions or comments, I'm in a position to where I love to give back. I'd love to talk to people about automation, what we've learned and reach out. Happy to just have the conversations and discuss things.
Tom Hardiman 29:48
Excellent. Shane Dittrich, House of Design Robotic Solutions, check them out. Appreciate you being here today, Shane. Stay tuned for another edition of Offsite Insights coming soon.
Don't Miss Our Upcoming Events!
Join the leading companies and professionals from across the offsite construction industry at each of this year's Offsite Construction Network events. With summits and expos taking place across North America in 2025, it's never been easier to connect with and learn from offsite construction manufacturers, designers, builders, and suppliers from the United States and Canada.
Subscribe today to get the latest updates on future events from the Offsite Construction Network.