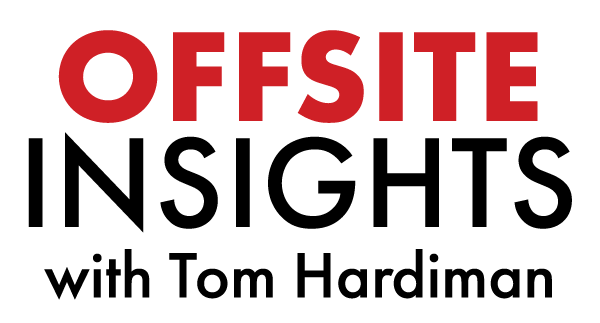
Exploring Transitional Housing from a Modular Design Perspective
An interview with Stuart Emmons, Principal, Emmons Design
Stuart Emmons joins Tom Hardiman to discuss his latest project that is a universal studio unit. The goal is to find ways to build a unit really fast while still having the same great quality and design. He also discusses his advocacy for the homeless population.
Interview transcript
Tom Hardiman 00:00
I'd like to thank today's sponsor for Offsite Insights. USG Structo-Crete brand structural panels are noncombustible mold moisture termite resistant, dimensionally stable panels for use and sub floor, roof deck or foundation wall assemblies. Structo-Crete brand structural panels meet the full criteria of ASTM E 136. For use and all types of noncombustible construction. Numerous one, two and three our fire designs are available for modular panelized and conventionally constructed buildings to meet virtually any application. The panels are easily cut with standard framing tools rapidly applied using mechanical fasteners and require no adhesive free installation. To learn more, visit www.usg.com/structocrete. Welcome to another edition of Offsite Insights. My name is Tom Hardiman and I'm your host for the show. I'm really excited today to have with me Mr. Stuart Emmons. Stuart, how are you doing today?
Stuart Emmons 01:07
I'm doing great, Tom. Nice to be here.
Tom Hardiman 01:10
Well, thank you for joining us. Real quick, Stuart is the owner and founder of Emmons Design, an architect firm in Oregon. Stuart, you want to start maybe just by telling us a little bit about yourself and your company, who you are and what you do.
Stuart Emmons 01:27
Sure. Before I became an architect, I was trained as a furniture maker and very involved in furniture production. That kind of morphed into construction. Then I became an architect, fast forward to 2009 and during the great recession we had to do things differently to attract or to go after public funded projects, housing projects. So, a friend of mine sent me kind of a joke email with containers, he said, we need to do something crazy. That evolved into, after I kind of laughed it at it, I got actually pretty serious about it and did a lot of research. We transformed a project from a traditionally design multifamily housing project to a modular housing project. We did not receive funding, but the city of Portland, Oregon, awarded us a contract for me to do a full blown study of traditional site built construction versus modular construction in anticipation of future projects. The year after that we did win the first modular affordable housing project, I think, in the Pacific Northwest.
I've been in the modular space for over a decade now, my passions are housing, homeless, and affordable housing in general. I'm actually writing an op ed, as we speak right now talking about how to reach ambitious goals. In our case, the governor of Oregon wants to do 35,000 units a year, an 80% increase, obviously, in California, this has been going on and the numbers are quite a bit bigger than that. The only way we're going to get to those numbers is if we think differently. I've worked on many modular projects, I've worked inside one startup company and one established modular company. So, I'm not just an architect, I'm very interested in business models and production, streamlining production to get as many units built as we can for the least unit cost.
Tom Hardiman 04:07
Well, you just kind of answered my next question. I was going to ask you, what got you interested in modular and what excited you about it? It sounds like it was a random email about containers that kind of triggered the thought process.
Stuart Emmons 04:19
It was. And then I looked at the container projects in London and in Holland, and I went, Wow, they're pretty cool. And my first design was containers and found the spacing didn't work. When I was at Blockable, about eight years after that, I went back to the eight and a half foot wide module and tested that in multifamily applications and I've graduated from containers. I just don't think the sizing works for especially multifamily housing.
Tom Hardiman 04:53
Okay. You mentioned you do a lot in housing. We've known each other for several years now and for as long as I've known you, you've been a pretty passionate advocate about addressing homelessness. Obviously, that plays into your desire for modular you think that's a good solution for cities.
Stuart Emmons 05:19
Portland’s been in the news a lot and when people come to our city it's appalling. The sidewalks and along the freeways here and the tents are just all over the place, but it's not just here. It’s every city on the West Coast I've been to has the same issue and maybe Los Angeles, the numbers are astronomical. So obviously I kind of point to the glacial pace of innovation and housing as being part of the problem. Yeah, there are other problems we know about social services and mental health institutions closing down and all that. But the other thing that we can do from our end is to step up that pace of innovation and housing and coming up with units like the old SROs back to the turn of the century, to get affordable housing for people on the street with very low incomes.
Tom Hardiman 06:27
Yeah, I think we had a meeting, Modular Building Institute, I should say, had a meeting in Portland, it's going back over a decade ago, and I was personally a little shocked about the number of homeless people I saw then. You’re right. I just got back from San Francisco, we've had a meeting in Sacramento, in Denver. We're seeing it everywhere and it's a huge and growing problem. I hope it's an issue that our industry can help address. Something I saw on your website that I don't think I've seen on any other architects’ site or any other contractor site, you have a whole section dedicated to the homeless on your page I noticed. So, kudos to you for being a passionate advocate. There needs to be more advocates out there. What is it about modular that you think makes it a good fit to address homelessness? Is it just getting that cost down? Is that the key thing?
Stuart Emmons 07:27
Well, it's a couple of things. First of all, can you imagine walking around the cities of the United States and not have tents? I mean, what a wild concept that would be and it would be so transformational, just to the psyche of our whole country to not have this issue. Where we can go focus on other things, getting people safe, warm and dry actually would save a lot of money on the on the back end. I think it has to do with certainly unit cost and I think there are ways in the modular world and that's what I'm working on right now is streamlining design and production. So, we can get our unit costs really significantly down below site costs. We've got room to grow in that area to improve in that area.
The other thing is time. In California, when we were there last year working on hundreds of modular units for homeless, the state of California has a program that originally was designed for transforming hotels for homeless, but now is being used for new construction. They said you get one year from when your funding is approved to when the certificate of occupancy needs to be pulled. Well, you can't do that with a traditional, so it's kind of cool for us because it's kind of forcing the hand to modular. You have to go modular to be able to achieve that deadline and then just humanistically. I'm working on a site-built project and it gives me a reminder of why I'm going modular. I keep saying I think after this project, I'm done with site built. I am over three and a half years on this project since I started it, and we're putting the siding on. So that equates to funding, cause inflation, interest rates going up, of course, point and time thing, but also humanistically if you have some person on the street a one year is a very different animal than three years. It could be a life and death issue. So, the cool thing about modular is we can get unit cost down and we can especially speed up delivery.
Tom Hardiman 10:23
Yeah. Then just a little side opinion here for me. I do think sometimes society gets in our own way. We said, well, it's more than just housing, it's health care and mental health and all these other things. So, we do nothing. Instead of a well, we know housing is a really good first step. Give them a safe, warm place to stay and then let's address the other health and mental issues. I think sometimes we use that as an excuse, like, well, just building housing isn't going to solve the problem. Well, no, of course not, but it's a heck of a good start.
Stuart Emmons 11:04
It is. I mean, this op-ed, I'm writing, I'm expecting a lot of blowback from the services crowd, and a lot of them who are good friends of mine. When I ran for city council in Portland, I came pretty close to winning, and maybe it's just as well, so I can focus on modular housing. I interviewed a lot of people on the street then I tried to put myself in their shoes and said, How do you do anything if you can't lock up your goods? If you know and women’s cases there's no privacy. There were a lot of prime issues and whatever, we have children out there. How do you get ready to go to a job? I mean, you can't work because your stuff is sitting in a tent that everybody can steal while you're at your job. So, it's a human dignity issue. Having a safe, warm and dry place with a door lock is key to stepping forward to everything.
Tom Hardiman 12:14
It’s not the final, but it is a big step forward.
Stuart Emmons 12:17
It's a huge step forward. It's not going to fix everything, but it's sort of the baseline.
Tom Hardiman 12:24
Well, again, kudos to you. How many people are going to go out and interview homeless people? Most people turn a blind eye or walk across the street, myself included. I've done it many times just go out and talk to them. That's great.
We kind of got into that issue, but that's fantastic that you're an advocate for that. I did see some of our industry, some of our members are doing more projects for in Canada, I think they're referred to as social housing. There was a large homeless shelter built in Los Angeles recently, and it might have been container based. The Hilda Solis center, we had several members involved with that one, so it was good to see these public funds starting to think a little more creatively and how they can use our industry to help get people off the streets.
Stuart Emmons 13:17
Right. I mean we've been talking a lot down in California about having architects come in with sometimes star architects, one project we were working on and coming up with projects where the units are not optimal for modular. So once again, I'm into building as much housing as we possibly can. So I'm really trying to encourage people in our industry to come up with a product. Come up with units that really are great to produce. Very efficient to produce wet walls, and where we can build them ideally in two days, then come to the architects with this sort of standardized unit design. I think that would help really speed up the delivery of the projects, get the unit cost down and great for our industry as well.
Tom Hardiman 14:15
Boy, we've talked about these standardized designs for quite a while on everything the hospitality industry wanted us to come up with a standard wood frame, you know, hotel room, and it's like, Wait, you're the industry, you tell us what you want, you standardize it we’ll build it. But yeah, you're right, if there was a couple of prototype standard units that we could crank out all day long. It kind of feels like we just kind of keep going in circles.
Stuart Emmons 14:54
Well, I think we're in a different spot even than we were five years ago. So when I was down in California, I did a huge code. I mean, everybody says, oh, it's the regulations that are causing all the trouble. Well, maybe, you know, they're complicated, but you look at the automobile industry. They have regulations and pretty significant regulations, too. And they figured it out. So, I went and really raked through the codes down in California, which are probably the most stringent in the country. Then I have been working on a studio unit that also can couple into a one and two bedroom unit that is universal, where all of it is fully accessible. It's easy to build and that's almost like us getting ahead of the game where we're marketing units. I used when I talked in DC you heard this Tom, we talked about selling Alfa Romeo. You can buy an Alfa Romeo, pick the color of the outside, the inside, maybe a few finishes and whatever, but the chassis is the same size. All the production is the same for every one of those cars. I think we should do the same for our units as well. I mean, I just lived this on two projects in LA where we were tweaking units again, and just doing an accessibility check and having accessibility inspectors out on the floor and whatever. We do this repeatedly for every project, it's just not necessary.
Tom Hardiman 16:34
It's maddening. We've had similar conversations at the national level when it comes to disaster relief. I can't tell you how many times we've reached out to FEMA, and said, instead of after every disaster, you send 1000, HUD code manufactured housing units, or RVs, or whatever. Design a better product that can go temporary to permanent, can stack easy, easily deployable, but that one is more wind, fire and disaster resistant than manufactured home. I'm convinced our industry can build a better product at a lower cost than what is being spent right now by the government. And have rapidly deployable, accessible, all those sustainably built check all those boxes. But I think you said it in the very beginning, the innovation in housing is just glacial pace.
Stuart Emmons 17:43
Yeah, I always like to say that. You look at high tech, and I'm looking forward to go ahead, just talk to people. Thank you, Tom, for introducing me to people at VPI and one of them mentioned the BMW plant down in Spartanburg, South Carolina. After hearing about that, I got to go see this. I mean, I've seen Autovol, but I really want to see this BMW plant to see how automated they are. Then you go back to the big dudes, I call them Game Changer changes, innovations in the housing world. I go back 100 years to drywall in 1916, and electricity and telephone in the early 1900s. And then the elevator, I mean, this stuff is a century year old.
Tom Hardiman 18:36
Roof trusses. That was a big break.
Stuart Emmons 18:38
Yeah, sort of. I mean, you're looking at houses getting built right now and then go back in your time machine 100 years ago, and you see the same kind of stick building and walls. I mean, there's not that much difference between now and 1923. So, I think that we ought to pick it up a little bit and the reason we need to pick it up is go look at our streets. That's one reason to pick up,
Tom Hardiman 19:11
That's homeless, then there's just the next level up, which is just affordable housing. People that are on that borderline of if it gets much worse, they're going to be homeless. There's a whole band of low income people that cannot find affordable housing.
Stuart Emmons 19:28
Right. And it's going to get worse to answer, you know, the trends, right?
Tom Hardiman 19:35
Yeah, fewer and fewer skilled laborers to build it and higher housing demands. Maybe we need to think about a different way of building homes going forward.
Stuart Emmons 19:45
You know, bringing robotics and computers then it's going to attract Gen Z and we're going to get younger work. I mean, our workforce is over 40 in the construction world. We've got to figure out how to get younger. I know they took woodshop at a lot of the schools, but you got to figure out how to attract a younger workforce and this is one way to do it.
Tom Hardiman 20:10
Yeah. My daughter is currently a sophomore in college and I said, if you want to drop out and be a plumber, electrician, I'm totally fine with that. You’ll be set for the rest of your life. Much less student loan debt. So, parents, push your kids towards the trades, towards a modular manufacturing plant. We'll train them up and keep them safe. There'll be busy and have that nice, long, productive career.
Stuart Emmons 20:38
I'll try that with my son after we get off the phone here Tom and see how that goes down. I think that goes back to the foundation of taking woodshop out of schools has caused a real problem and labor force for construction.
Tom Hardiman 20:57
Absolutely. Hey, let's shift gears a little bit. What advice or what best practices would you give to other architects who may be thinking about getting into the modular field, but they're not sure about it? What's a good starting point for them?
Stuart Emmons 21:14
I built stuff before I went and became an architect and also into the modular world, I went through a lot of factories and talked to people on the floor and talked to modular designers, but also the plumbers and the electricians, and what works best. Really understand all the systems, all the components that go into designing. So everyone says, what's the difference between traditional design, architectural design and modular design? Well, there's quite a bit. I mean, you can make the dimensions fit for modular that we can transport and so on. But there's another way you can make it even more sophisticated too, like wet walls and looking at how units are assembled, and penalisation. That sort of thing that would really reduce unit costs and make modular reach the goals that we all hope it can achieve. I mean, there's so much work out there and for modular housing we don't almost need to compete with each other. We should just work together and share, right?
Tom Hardiman 22:38
There's plenty of work out there. There's plenty of housing that needs to be built.
Stuart Emmons 22:43
I mean, there in California, it was just unbelievable. We have too few plants down there, too few people in the modular space to accommodate the need. Then in the Pacific Northwest we're still struggling to get a good number of factories in this area that our friends in Boise and Nampa have. We got some great plants out there. We got a great plant, Blazer here, but there's a much higher need than these that gives us a great opportunity.
Tom Hardiman 23:22
Well, you've got like two factories in Oregon. I'm sitting here in Virginia and I think we have one. So yeah, you're right. We need more factories and maybe that’s more manufacturing jobs. If any of our policymakers are out there listening, we'd be glad to help you incentivize new modular startups or workers in more factories.
Stuart Emmons 23:45
There's a potential modular startup in Portland coming up. We've been in talks and whatever. I was in a startup, just north of here in Vancouver, Washington and Seattle, back in 2017. So, it's okay not to know everything. I mean, this is complicated, starting a modular company and getting marketing down to site construction all figured out and building a really great team, which I think is the number one thing you need for a successful modular company. Please reach out and then there are lots of good people who can and also, as I've done, Go into all the factories.
Tom Hardiman 24:37
A great tip, just go visit some factories, talk to people.
Stuart Emmons 24:41
The other tip is go look at modular installations, because I've seen a lot and there were some that didn't go real well, and that's okay to just learn from this. I've seen probably about 40 modular multifamily installations during different parts of the sequence. I've learned so much from that, and that goes back into architectural design, for instance, per unit. I looked at one project that took an hour and a half to install each box. How do you make that a half an hour? How does that impact the initial design of the unit?
Tom Hardiman 25:21
Well, Stuart, what's on the drawing board for you? What are you working on now?
Stuart Emmons 25:26
Well, Tom, we don't have any drawing boards anymore. Actually, I have a drawing board my dad gave me when I was 10 years old and he didn't know anything about architecture. He sure supported me and I really appreciate that. So on the drawing board, I have my home to unit that is this universal studio that I have designed. Fully accessible, but it's rapid to build. I'm also looking at cost. I was on one project where the kitchens for this is for a homeless population were for a family of four. I said, Why do you need all that? How do you reduce costs and get unit costs down? So, I'm working on the studio that also has a different size module that goes to the side of it for a bedroom or a bedroom on the other side. It's designed to be built in two days, and I'm looking forward to working with people on the famous drywall question in the next six months. I know people in the Bay Area are working on that. I want to figure out how to build a unit really fast, same quality, great design kind of like this. I've been in all these user group meetings where we're sort of building units for like four months, have weekly meetings, and they'd be happy to go look at some really cool units that are pretty well set up. If they can go pick the color of the kitchen and some finishes in the bathroom, maybe there's a bathtub or a shower, things like that. The general thing is the unit is set up and I think clients would really embrace that.
Tom Hardiman 27:13
Yeah, that's great. Get the keep the quality, get the cost and the time down. Right, you might be on to something there.
Stuart Emmons 27:21
Maybe we've been talking about it for a while. I needed to go through some more plants and my experience even in the last year down in California has been awesome. I have learned so much from this in factory experience and working with some really great clients down in California. I'm working with some really talented people and we've been talking every day about how to do this better. I think it's really paying off.
Tom Hardiman 27:54
That’s excellent. Well, speaking for myself, the industry's very glad to have you as part of it. Appreciate your advocacy for the homeless population. We could use a few more people like you out there being their champion and I appreciate your time today. Stuart, we're going to wrap it up with that unless you got any parting thoughts?
Stuart Emmons 28:18
No, but I'm really excited about the possibilities of modular going forward. I think we're in a really different place than we were back when I got into the space in 2009. I think we've learned a lot. We've gotten some really good companies. Some companies didn't make it. We've learned from them. I just think we're in a really good place and plus, parallel with us, we have a huge housing crisis in our country, that people are struggling for solutions. So, I think we have this solution or a solution that's really good, and I'm really looking forward to the next years and working in the modular space.
Tom Hardiman 29:03
Excellent. Well, thanks again Stuart Emmons from Emmons Design in Oregon. This has been another edition of Offsite Insights, be sure to check out the next edition. Thank you, Stuart.
Stuart Emmons 29:14
Thanks, Tom.
Don't Miss Our Upcoming Events!
Join the leading companies and professionals from across the offsite construction industry at each of this year's Offsite Construction Network events. With summits and expos taking place across North America in 2025, it's never been easier to connect with and learn from offsite construction manufacturers, designers, builders, and suppliers from the United States and Canada.
Subscribe today to get the latest updates on future events from the Offsite Construction Network.