AI, Faster Sets, and Automation: The Future of Modular Is at World of Modular
A sponsored article from the Modular Building Institute
Increased productivity, improved labor efficiency, and faster module production are available if you’re willing to embrace the latest facets of modular construction. Using AI, connection standardization, and robots, some companies are already embracing the future.
At the 2025 World of Modular, a few of these companies will share their secrets so everyone can help push the industry forward.
AI’s Impact on Productivity
If you’re unsure about artificial intelligence’s role in the modular construction industry, Sneha Kumari’s session, “The Productivity Paradigm: AI's Impact on Modern Construction,” is a must-see. As co-founder and CEO of Merlin AI, her presentation will provide real-world examples of how builders and manufacturers leverage AI to increase efficiency, reduce costs, and accelerate project timelines.
Merlin AI is an AI-powered enterprise system that aims to help project teams increase efficiency and reduce costs. One of its most powerful offerings is its estimating tool, which can generate estimates up to ten times faster, allowing builders to optimize their bidding strategies. It also has a configurator tool for modular factories that allows them to select and customize models based on predefined options.
“Traditional workflows in estimating, scheduling, and project management often involve manual processes, disconnected data, and inefficiencies that slow down production and eat into margins,” said Kumari. AI helps eliminate these issues, increasing efficiency, and it enables teams to make real-time decisions. “Whether it’s adjusting production timelines, optimizing material usage, or recalibrating estimates based on live project data, AI allows builders to stay agile and proactive.”
“In an industry where time and precision are critical, adopting AI isn’t just about staying competitive—it’s about setting a new standard for efficiency, scalability, profitability, and the ability to predict outcomes in offsite and modular construction.” According to Kumari, contractors and designers who adapt AI and similar tools are set to gain a significant advantage over those who don’t. These companies will then be able to scale, adapt, and perform better than their competitors. If you don’t want to be left behind, you’ll want to attend this session to learn more.
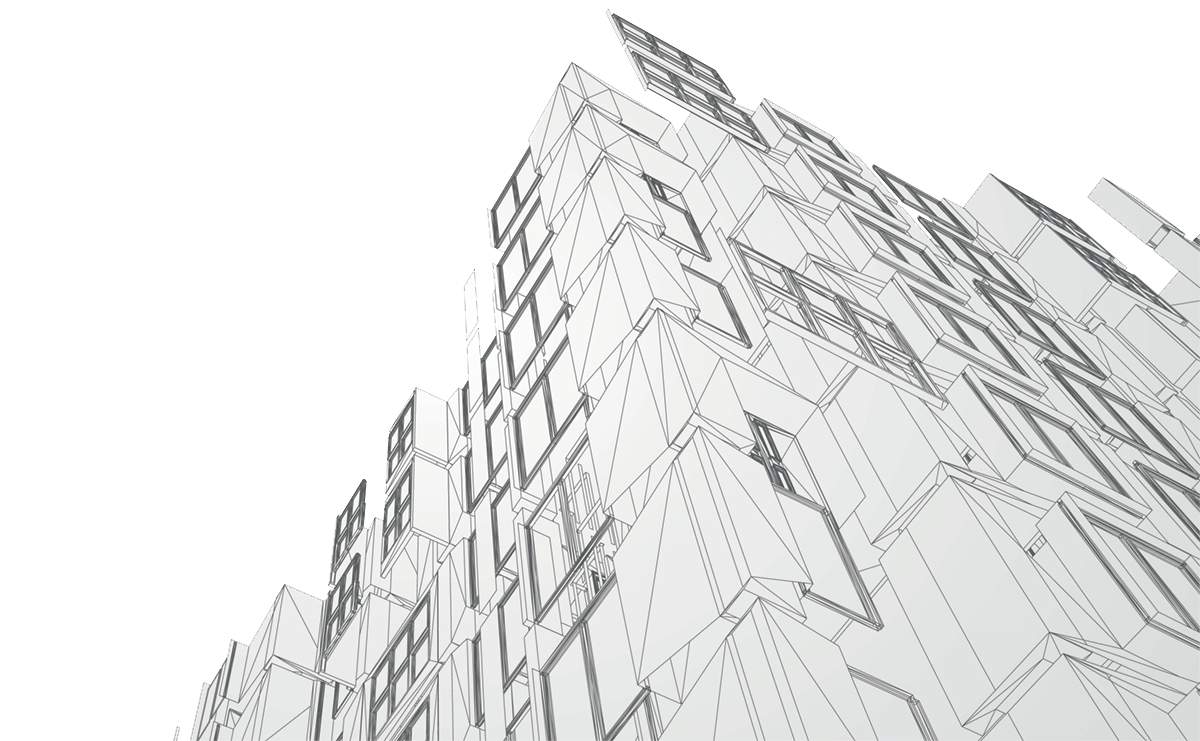
Hidden Costs of Field Labor Inefficiency
Cloud Apartments, a development company focused on multi-family housing, addresses field inefficiencies by redesigning their mechanical, electrical, and plumbing connections to simplify field installation. Cloud partners with factories, installation partners, and contractors to deliver its patented building system that saves on cost. Traditional modules are designed to have utility connections made in the field through the common corridor. Both vertical and horizontal connections are made after the unit has been set. The Cloud Connect system streamlines this work into a single connection point, drastically reducing field labor time and costs.
Cloud Apartments grew out of the idea that if apartments were standardized and value engineered in a precise way, cost savings could be created without compromising the renter experience. “The fact that we have such a drastic gap in between supply and demand in this country around housing is unacceptable, and that's what has driven our mission from the get-go,” said Apoorva Pasricha, COO of Cloud Apartments.
Through data analysis of thousands of module sets, Vice President of Construction Matthew Rapa identified several areas where integration between the factory and the field could be improved. Based on this analysis, he developed a unique solution with company founder Curtis Wong that simplifies field connections, saving time and money.
“CloudConnect incorporates alignment into the shaft as a key point, and the MEP system we've developed is a telescoping push-fit plate that allows us to flex in the up and down or Z direction,” Rapa said. “As the upper module sets on the lower module, the plates will align and mildly compress until we finish the mechanical fastening around them. The connection is 90% made until it’s mechanically fastened.”
“CloudConnect reduces the time trades have to spend on site,” said Pasricha. “And the installer can complete the installation by simply fastening four bolts. So, you're able to create a dent in the field costs.”
Perhaps more important than their specialized connection system is the mindset shift required to think like a factory, knowing exactly how much time and materials each task takes. “Can we start changing the narrative of conventional pricing to something more takt-time-based like manufacturing?” asked Rapa. “I've worked in conventional and modular construction and have graphed actual data on both types of projects and different ways to do things. I think there's definitely something here that can create more success for the entire industry if the lens shifts a little bit.”
The goals of their presentation, “Hidden Cost Driver in Modular Construction: Rethinking Field Labor Efficiency,” include introducing their innovative technology to the industry, sharing cost data to demonstrate its impact on construction costs, and seeking feedback from industry players, including designers and developers.
“Modular construction promised to save money,” said Pasricha. “And most of the projects you see built through this method have not saved on cost. Part of the reason is that when you do a modular project, the hard costs break out to about 25% in the factory and 75% in the field. That ratio must be flipped if you want to save on costs by going modular. And to flip that ratio, all your innovation has to focus on addressing inefficiencies in the field.”
Attend their session to learn more about the specifics of the connections.
Accessible Automation
Companies hesitate to invest in automation for various reasons, including the lack of a market for their work and the effects of the skilled labor shortage. In their presentation, “From Vision to Reality: Developing a Roadmap for Accessible Automation,” Jan-Christoph Bruhn, Head of Sales and Key Account Management for KUKA Assembly & Test, and Cooper Lane, Vice President of Sales for Reko Automation Group, will make the case for a spectrum of automation options that help take fear out of the equation. The two will discuss their experiences in Germany and North America to highlight the benefits of automation, whether it’s for a single process or an entire manufacturing plant.
KUKA, headquartered in Augsburg, Germany, is known for building robots for various industries. For the past five years, it’s been involved in modular construction in Europe, building automated plants in the United Kingdom and Germany. They focus on steel-framed buildings, which are more popular than wood-framed buildings in Europe.
Reko is an automated systems designer and provider headquartered in Ontario, Canada. It has been in business since 1976 and has mainly focused on automotive manufacturing. Recently, it diversified into offsite construction. Reko provides production systems for steel-framed buildings, wood-framed buildings, mass timber, and composite materials.
“We strongly feel that if you are setting up a proper manufacturing facility with tools like what Reko and KUKA provide, you should be making modular units for cheaper,” said Lane. “You should be taking advantage of innovations in production manufacturing. The strides they've made in automotive manufacturing over the last 50 years, utilizing robotics and automation, have driven the cost of production down. We feel that with the proper application of automation in the construction space, we can do the same thing, which will drive utilization up and help foster more innovation in this space.”
During their presentation, they will address several key points, including:
- The benefits of automation
- How to tell when you’re ready to begin using automation
- The type of environment you need for automation
- How job descriptions are changed when automation is implemented
Bruhn believes that one reason European companies haven’t invested in automation is because the market isn’t strong enough to handle the number of modules an automated factory could produce. “There are no companies available who are buying 20 multi-family buildings with 50 or 60 apartments in each one because the investment doesn't make sense based on interest rates and the rent you can charge in Germany currently,” said Bruhn. The skilled labor shortage is also creating issues, Bruhn said, as many companies cannot find the welders necessary to build steel buildings.
According to Lane, some builders still believe that automation can only be useful if they repeatedly produce the same product. “They automatically discount the effectiveness of automation. But automation has come a long way and can be far more flexible,” Lane said.
While automation won’t cure all the ills of construction, it is an option many are considering more closely.
Learn More at the 2025 World of Modular
With dozens of breakout sessions led by industry leaders, the 2025 World of Modular promises to be an unparalleled opportunity to learn more about the present and future of modular construction.
See all speakers and presentations from the 2025 World of Modular.
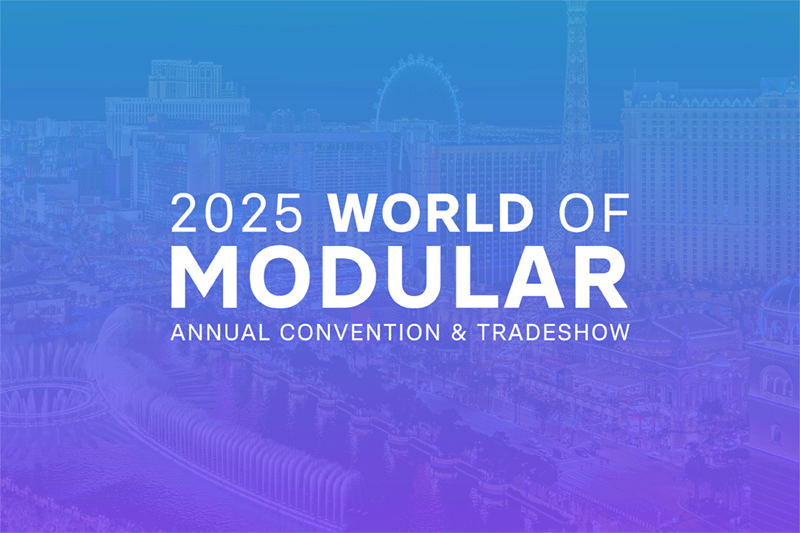
About the Modular Building Institute: As the Voice of Commercial Modular ConstructionTM, it is the mission of the Modular Building Institute (MBI) to expand the use of offsite and modular construction through innovative construction practices, outreach and education to the construction community and customers, and recognition of high-quality modular designs and facilities.
Don't Miss Our Upcoming Events!
Join the leading companies and professionals from across the offsite construction industry at each of this year's Offsite Construction Network events. With summits and expos taking place across North America in 2025, it's never been easier to connect with and learn from offsite construction manufacturers, designers, builders, and suppliers from the United States and Canada.
Subscribe today to get the latest updates on future events from the Offsite Construction Network.