Affordable Housing Now: The Industry’s Best Bring New Solutions to World of Modular
A sponsored article from the Modular Building Institute
In the US there is a shortage of more than 7 million affordable homes for the 10.8 million plus extremely low-income families, and there is no state or county where a renter working full-time at minimum wage can afford a two-bedroom apartment. The situation isn’t much better in Canada, where a 2023 report showed a need for 4.4 million affordable homes.
While modular building insiders have known for years that it can be an effective solution to address both the quantity and speed of development that’s needed, the word is slowly spreading to more mainstream audiences. Three presentations at the 2025 World of Modular (WOM) in Las Vegas hope to provide insight and direction for those seeking a real solution to the crisis.
Unlocking the Potential of Pocket Neighborhoods
Eisa Lee, Partner Architect at xL Architecture & Modular Design in Toronto, Canada, says a pocket neighborhood, a small community within the larger community that takes advantage of smaller infill land areas, can help fill some of the housing shortage. Her presentation will look at a current pocket project, which is being built by a church community and involves filling an unused parking lot with tiny homes, as a showcase for what communities can do to help.
Her design company serves as a go-between for project designers and modular factories, providing guidance with factory set-up and design, process improvement, and production design. “We've worked closely with and understand the entire process of designing for manufacturing and assembly and how to get them into the initial schematic design stage,” said Lee.
Modular construction plays a key role in developing these communities because of the repetitious nature of the tiny homes. Lee compares it to buying a pre-built shed at a big box retailer, where manufacturers have several models to choose from and residents or developers can select which ones they want. Since structural building codes are similar across all locations, it streamlines development because the only design required is a community or site plan and utilities. “Essentially you complete the site work, deliver the tiny homes, and then connect the services, and there you go.”
Site selection is key as the community must blend into its surroundings. “You don't want to build a tiny home pocket neighborhood in the middle of 30- to 40-story condo buildings. And then again, you don't want to be building a 30- to 40-story condo in a neighborhood where it's all single-family or two-story homes.”
Lee said developers of potential pocket neighborhoods should research them before determining if they make sense for their specific project. They’ll need to know why they’re a good idea and why people would choose to live there. The focus should be on the quality of living and building relationships with the residents. The next step is to engage with a designer who can help them see how to develop a sense of community for the owners because otherwise, it’s just a bunch of people living in a dense area.
Her presentation at WOM will help developers, landowners, and modular manufacturers understand the benefits of pocket neighborhoods and how to implement them in their areas. Lee hopes the session creates connections for attendees to collaborate and create more great communities.
Collaboration Strategies in Affordable Housing Project Delivery
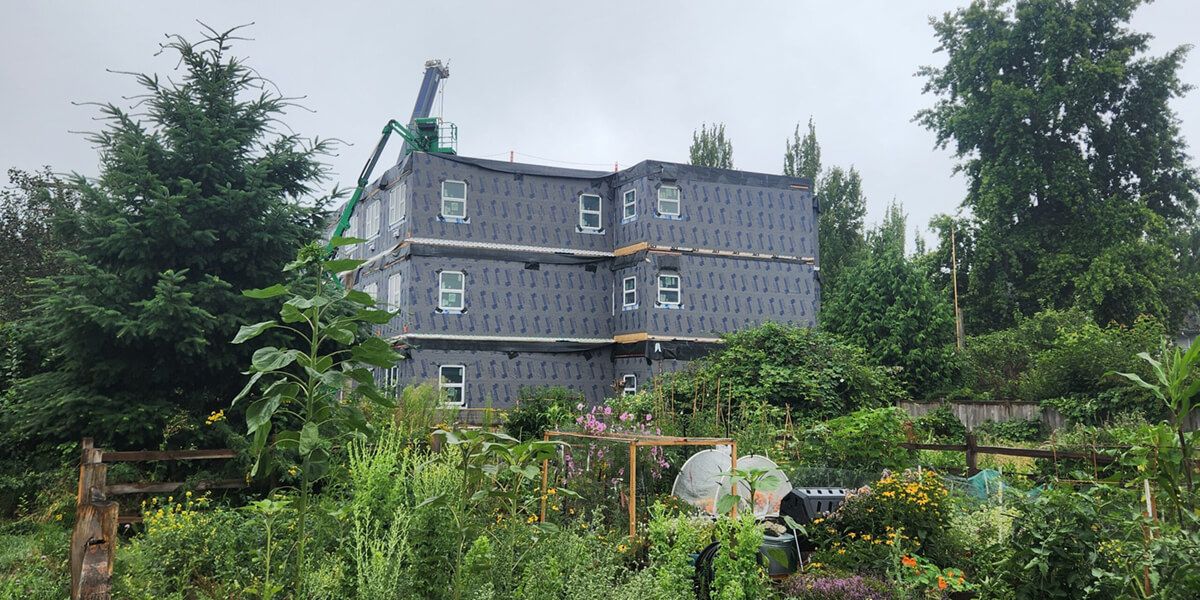
Rhys Kane, Director of Business Development for ROC Modular, and Jerry Rynda, Director of Business Development and Marketing for Buttcon Holdings, will be presenting a case study that highlights the importance of bringing a project team together early and working collaboratively to meet the stated goals. The Steveston Highway Turning Point Housing Society project is currently under construction in Richmond, British Columbia, Canada. It will be a three-story wood-framed modular multi-family building, consisting of 25 units. ROC is the unit manufacturer, Buttcon serves as the general contractor, and TASU Construction is installing the modular units.
Collaboration is key to any modular project. “There's so much upfront design and planning that has to be done and so many decisions that need to be made prior to fabrication, that if you don't have transparent collaboration with the client, architect, consultants, fabricator, and the builder, it almost always leads to problems,” said Rynda. “Because if the architect doesn't understand that they need to have as-built drawings completed before procurement, that causes a train wreck. Also, the client needs to understand that they can't make any changes to the modules once fabrication starts. You need seamless coordination, streamlined processes, problem-solving, change management, and quality assurance.”
Buttcon starts each project with a responsibility matrix, outlining responsibilities for all the primary stakeholders, including trade contractors. When key responsibilities are clearly identified, said Rynda, it frees the team up to focus on getting the project completed on time for the right price, which is the client’s main objective.
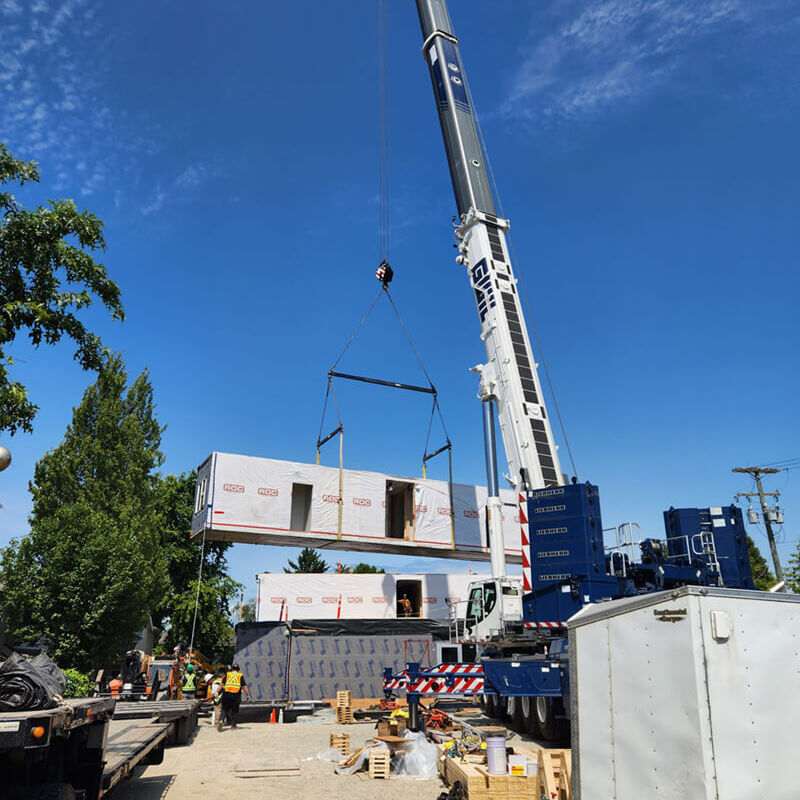
Kane said it’s important to get the modular factory engaged as soon as possible so he design can be tailored to fit modular construction from the beginning. He encourages clients and designers to commit to modular as early as possible and then engage the factory. “We can then provide all the rules around modular design, what's most efficient for the factory, and what's going to help the project end with a good result,” Kane said.
Collaboration can also help with funding and cost management. With public funding sources there can be numerous requirements that need to be met to qualify, so working together on those from the beginning can help smooth out the process. Rynda said, “I think it is critical to have stakeholder alignment, ensuring that everybody has a clear understanding of the project goals, priorities, and timelines.” This includes details like sustainability targets and the design specifications required to meet the project budget.
Of course, conflict can occur on any project, so having a conflict resolution process is necessary to address changes and prevent delays. Rynda said, “It’s easy to butt heads or be negative. Collaboration is like a marriage; you must work together. If not, you’re going to kill each other.”
Kane hopes their presentation provides a realistic view of a factory and general contractor working together, both the good and the bad. Rynda hopes to attract more general contractors to embrace modular construction and provide some tools for them to use on current or future projects.
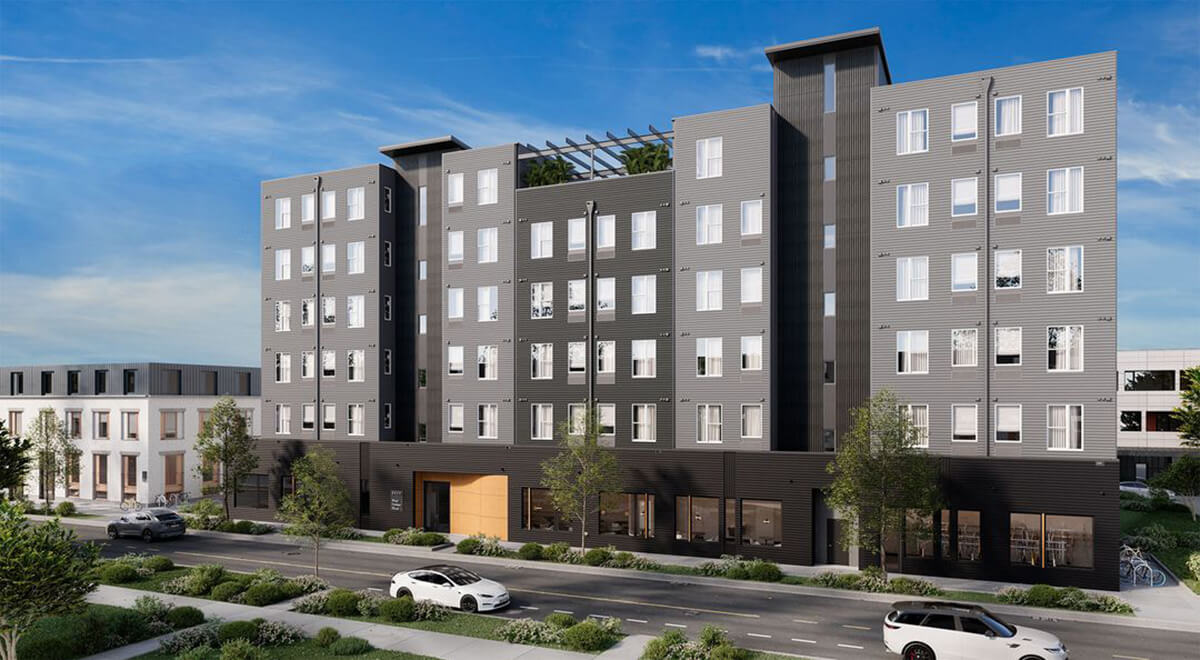
Modular Affordable Housing Case Studies
Adam Berger, owner of Adam Berger Development, and Christopher Herr, Design Director, will be offering a case study on their West Holden Place project: a six-story, 77-unit, multi-family development in Denver, Colorado. Set for completion in March of this year, the project showcases how modular construction can solve affordable housing challenges by reducing costs by 20-25% and cutting build time by about 40% compared to traditional site-built projects.
For Berger, modular construction isn’t just about efficiency, it’s a solution to one of housing’s biggest challenges: affordability. His firm is proving that high-quality housing can be delivered faster and more cost-effectively, meeting the growing demand in cities like Denver.

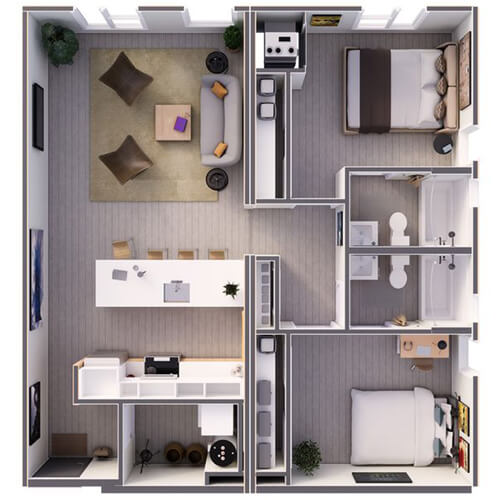
The firm’s success is driven by three key factors—a vertically integrated business model, a focus on efficiency and repeatability, and maximizing offsite construction—allowing them to streamline operations, reduce costs, and accelerate project timelines.
“The north star for us, whether modular or site-built, is creating a high-quality living experience,” said Berger. “Residents don’t care if it's modular—we do, but they don’t. They just want a great place to live.”
Adam Berger Development operates with a unique business model, serving as owner, developer, architect, and general contractor. This model enhances efficiency and eliminates unnecessary mark-ups, enabling the firm to work directly with nonprofits who may have land but lack the expertise or resources to bring a project to life, taking the lead on everything grom financing and design entitlement to construction.
To fund projects, Berger works with the Colorado Housing Finance Authority and other non-profits, supplementing that funding with private sources. Colorado has embraced modular building, offering financing for modular factories and projects, which Berger attributes to the state’s short construction season, labor shortages, and the benefits modular building provides.
Efficiency and repeatability are equally critical to Adam Berger Development’s success. By working with the same team across developments, from trade contractors to financing, and utilizing a design that is easy to replicate, reducing uncertainties and streamlining construction. By maximizing offsite construction, the firm ensures a faster, more predictable development process. With everything but the corridors, utility connections, and exterior façade built in the factory, their team delivered and set 50 boxes for West Holden Place in just seven days.
“Before construction, we developed a detailed plan clearly outlining what was offsite versus onsite, not just for subcontractors to review and price, but also for permitting and inspectors to understand their scope,” said Berger. “Working with different jurisdictions can be complicated since site requirements are often dictated locally, while the modular units fall under state regulations. Building the necessary relationships with both the City of Denver and the Colorado Division of Housing was key to ensuring a seamless approval process and keeping the project on track.”
Berger’s presentation will show project teams exactly how modular construction can be used to create high-quality affordable housing with a strong model that is easily replicated.
All three of these presentations will appeal to many in the industry, whether new to modular or well-seasoned. All offer real-world examples of successful projects that attendees can take back and implement in their markets. The overall goal is to help push the needle and encourage the adoption of modular construction for affordable housing, a critical mission in both the US and Canada.
Learn More at the 2025 World of Modular
"My hope is for attendees to leave [World of Modular] with a clearer understanding of...the enormous potential modular systems have to deliver impactful housing projects," said Lee.
See all speakers and presentations from the 2025 World of Modular.
About the Modular Building Institute: As the Voice of Commercial Modular ConstructionTM, it is the mission of the Modular Building Institute (MBI) to expand the use of offsite and modular construction through innovative construction practices, outreach and education to the construction community and customers, and recognition of high-quality modular designs and facilities.
Don't Miss Our Upcoming Events!
Join the leading companies and professionals from across the offsite construction industry at each of this year's Offsite Construction Network events. With summits and expos taking place across North America in 2025, it's never been easier to connect with and learn from offsite construction manufacturers, designers, builders, and suppliers from the United States and Canada.
Subscribe today to get the latest updates on future events from the Offsite Construction Network.