Azure: Creating Affordable and Sustainable Housing with 3D Printing
An exclusive article from the Offsite Construction Network
There’s no question about it: Finding affordable housing is difficult in today’s economy. Supply chain disruptions and other issues have caused prices to soar, leaving many buyers priced out of the market.
Los Angeles-based company Azure Printed Homes has a potential solution. Its goal: to help people find affordable housing with 3D-printed homes.
Recently, Azure has started to build 3D-printed homes with a specific group of people in mind.
Building Homes for Veterans
When military veterans return home, many have difficulties finding housing. Transitioning to civilian life can be complicated, and some veterans come home contending with new, service-related disabilities and challenges.
Azure, in an effort to help mitigate this housing issue in Southeast California, announced plans to create a community of 3D-printed homes in Twentynine Palms, home to the largest U.S. Marine Corps base in the U.S. The development, called Veterans’ Village, will include two-bedroom homes with 900 square feet of living space each. Gene Eidelman — the co-founder of Azure Printed Homes — says the objective is to build high-quality 3D-printed buildings by reducing costs and improving environmental affability.
To help fund this project, Azure has applied to receive funding through the California Energy Commission. This office offers grants to companies employing advanced technologies to promote clean energy and efficiency. Eidelman says receiving the grant would reduce construction costs and ease the strain on all parties.
“We were proposing more expensive solar panels that are more efficient,” he says. “So, the grant would pay for things we can do that sometimes our clients can’t afford.
“It’s good for the industry. If the county or state can assist in making projects more energy-efficient, then it’s a win-win.”
Making Use of Otherwise-Wasted Plastic
These cozy, 900-square-foot homes are intended to be build-to-rent (BTR) structures, but their construction doesn’t come from conventional methods. Azure Printed Homes uses 3D printers to build its houses, and the company will construct the homes for Veterans Village from recycled plastic.
Eidelman says the amount of plastic needed for the project equals about 750,000 water bottles — about 20,000 pounds. Luckily, there’s an abundant supply of raw material.
Plastic waste is an issue in nearly every industry in the United States. Research shows about 73% of Americans’ plastic waste goes to landfills. Using recycled plastic makes the Veterans Village much more environmentally friendly.
Discovering The Benefits of 3D-Printed Homes
One of the most significant advantages of modular building is the short timelines. Most of the work takes place in an off-site facility. About 80%-90% of modular construction occurs before it arrives at the client’s destination. Once the home transfers to the building site, Martin Schmädke says the only tasks left are leveling the ground and connecting water and utilities.
Costs
First, Eidelman says the costs of 3D-printed homes are much lower than typical stick-built structures. With a 3D printer, builders can create just about any design. There is less material waste and a reduced need for traditional construction methods, such as scaffolding and formwork.
Another cost-cutting measure is the selected materials. Many contractors come in over budget, but Eidelman says using recycled plastic lowers the costs.
“We don’t use any lumber, we don’t use any roofing material,” he says. “Recycled plastic is less expensive than those two things.”
Schedules
When builders don’t have to worry about the weather, they can shore up the timelines and make the process quicker. Recent supply chain disruptions have made building homes on schedule much more complicated. The troubles have extended lead times by months for many products, causing backlogs worldwide.
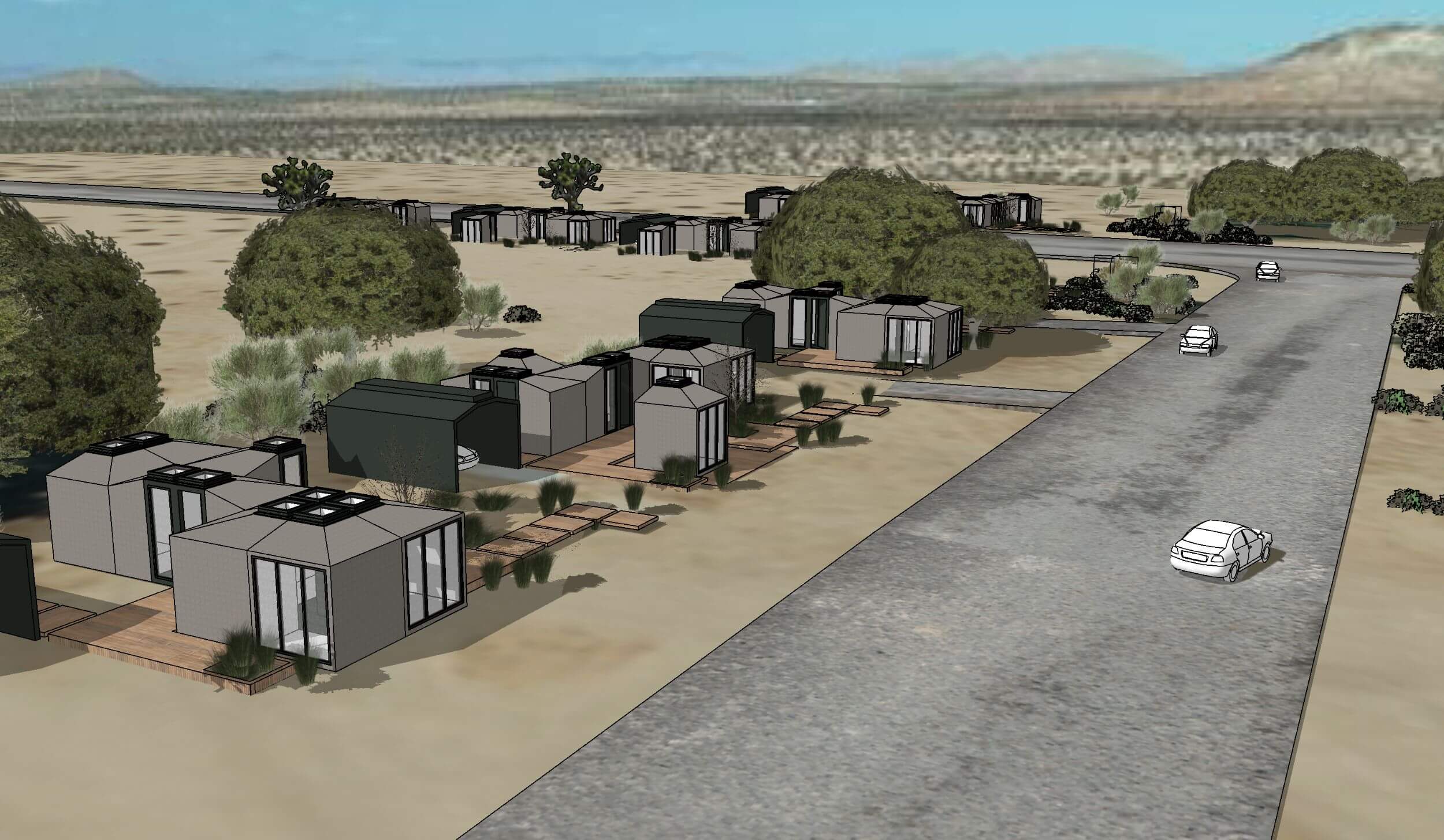
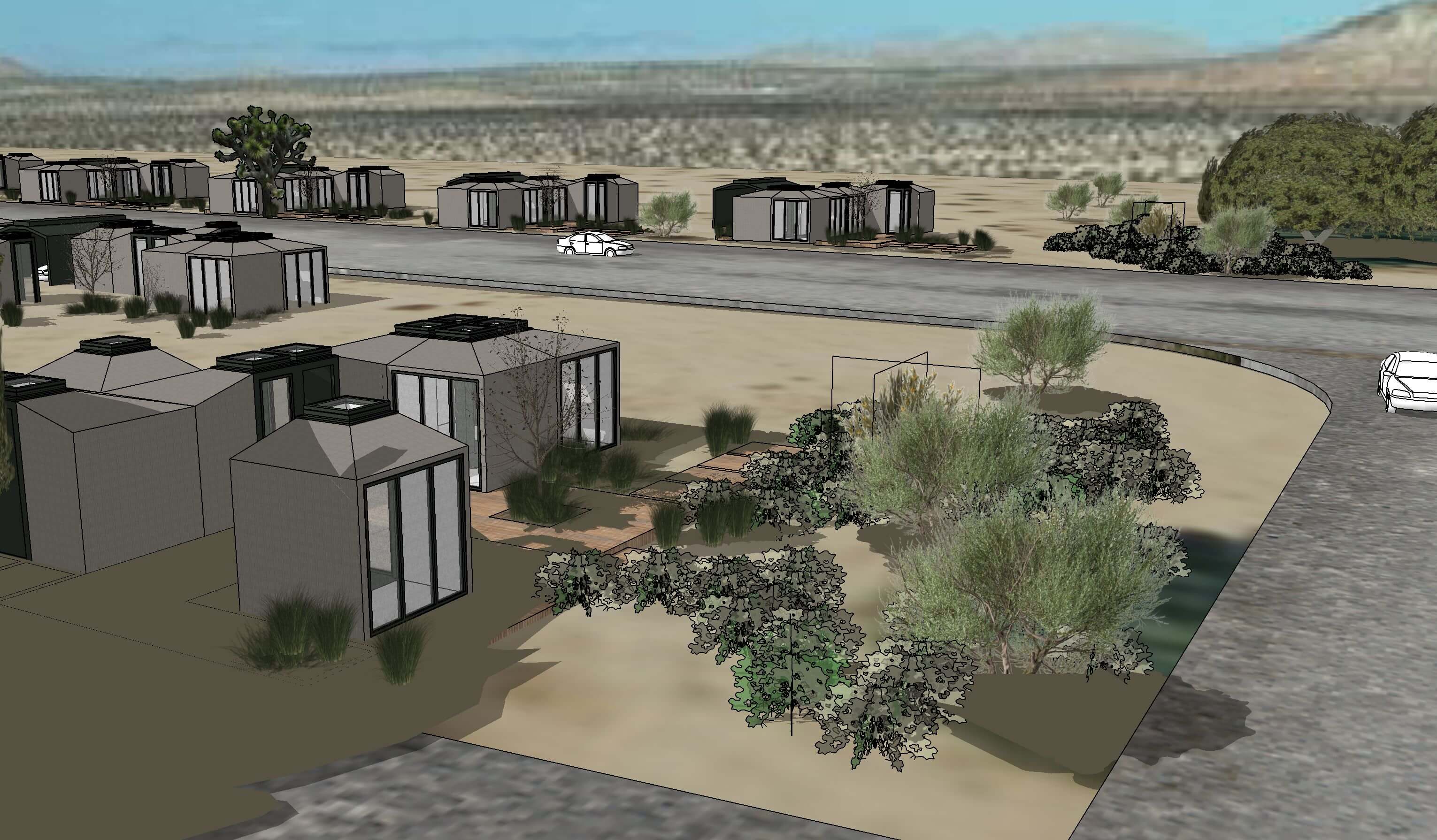
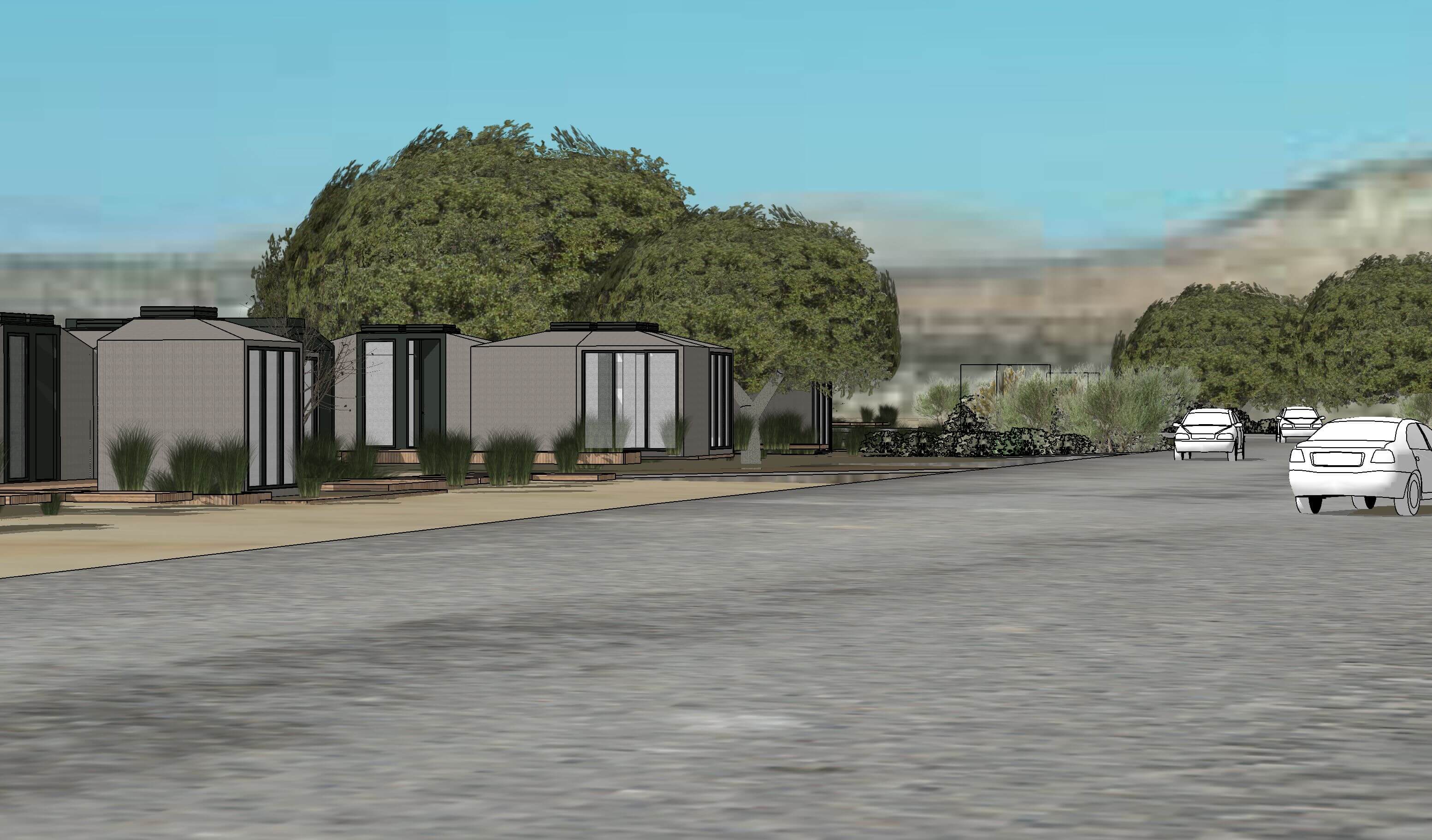
3D Printed Home Community Concept by Azure
When builders don’t have to worry about the weather, they can shore up the timelines and make the process quicker. Recent supply chain disruptions have made building homes on schedule much more complicated. The troubles have extended lead times by months for many products, causing backlogs worldwide.
“What helps us to think this through is the fact that we’re contractors,” Eidelman says. “We’ve looked at how do we accelerate the timeline and how do we lower the cost?”
3D-printed construction speeds up timelines and makes building much easier despite modern challenges. Eidelman says factory-printed homes will significantly benefit the Veterans Village community.
“Usually, a project of that size to build the 30 homes takes 12 to 18 months,” Eidelman says. “In our instance, it’ll probably take about six months to get all the permits.
“But once permits are obtained, the site work is about three months. And homes will be printed in our factory at the same time.”
Safety
Construction can be a dangerous occupation. A laborer or architect can get injured on the job site in numerous ways. Tall structures often lead to falls — in fact, over 33% of construction deaths happen because of falls.
Using 3D-printing methods leads to safer outcomes because construction occurs in a climate-controlled facility. There are fewer concerns about common on-site safety hazards.. For example, over 33% of construction deaths happen because of falls. With no need for scaffolding and the relative safety of an offsite manufacturing facility, these risks are minimized.
The materials used in 3D-printed buildings are also safer to build with. With lighter construction materials made with recycled plastic, Azure’s workers don’t need to haul heavy loads and there are fewer strains on machinery.
Sustainability
Sustainability is a significant factor in the minds of many in today’s construction world. The built sector consumes a lot of energy and releases greenhouse gases (GHG) during production. Martin Schmädke says Huga ensures long-term use by constructing homes based on the area’s climate.
For example, Martin Schmädke says artificial intelligence (AI) is essential to construction. Huga uses AI to study the sun and the environment and uses the data to determine what materials are best for the particular location it’s building.
Various locations deal with different threats of weather and geological issues. For example, Californians face earthquakes while Floridians deal with hurricanes. Homes in coastal areas often abide by zoning laws and use risers to reduce the risk of flood damage. Martin Schmädke says reinforced concrete makes Huga’s materials sustainable in numerous climates.
Typical houses have a life span of 70 to 100 years, depending on maintenance, weather events and other factors. However, Huga uses reinforced concrete because these structures last hundreds of years. Martin Schmädke references concrete buildings in Rome that still stand after 2,000 years.
Martin Schmädke says reinforced concrete is vital in the U.S. because of soil conditions. For example, there may be radioactive radon. Using concrete helps keep the gas inside the soil.
Concrete protects customers from outside forces like radioactive material and living creatures. The structures are termite- and insect-proof, so clients don’t have to worry about bugs compromising the building in rural areas. Huga’s homes are also bulletproof, giving clients peace of mind no matter where they live.
Labor Shortages
3D printing has allowed Azure to cut through labor shortages and meet client expectations. Eidelman recalls a developer who wants to build 20 units a month despite the market conditions.
“That’s almost impossible to accomplish with traditional construction,” Eidelman says. “I really think that for the offsite construction industry, it’s a great opportunity.
“Crisis creates opportunities. Being able to deliver units quickly helps developers return an investment.”
Creating 3D-Printed Homes to Help the Planet
Eidelman understands the housing crisis in the U.S. and worldwide, so he sees 3D-printing homes as a tool builders can use to mitigate the housing and environmental crises. And where once these houses were plastic bottles, they too are intended to be reused down the line.
“The element of the circular economy is not just to make things out from recycled materials but also at the end of life to use it for something else,” he says. “Our product is designed to be recycled when you know the useful life is used up.”
About the Author: Rose Morrison is a freelance writer and designer with a background in construction You can contact her at rose@renovated.com.
Don't Miss Our Upcoming Events!
Join the leading companies and professionals from across the offsite construction industry at each of this year's Offsite Construction Network events. With summits and expos taking place across North America in 2025, it's never been easier to connect with and learn from offsite construction manufacturers, designers, builders, and suppliers from the United States and Canada.
Subscribe today to get the latest updates on future events from the Offsite Construction Network.