A View Towards the Future: Building with Virginia Tech’s New Low-Carbon Hardwood CLT
An exclusive article from the Offsite Construction Network
Constructing an observation tower for the city of Radford gave Virginia Tech students a unique hands-on learning opportunity. Commissioned in 2018, the New River Train Observation Tower project challenged graduate architecture and design students to source, design, and build an environmentally-friendly, handicap-accessible modular structure for public use. The clients were the City of Radford, the Radford Heritage Foundation, and the Glencoe Museum, and the purpose was to highlight the region’s train history by giving visitors a dramatic view of the old Norfolk Southern Rail line.
Associate Professor Kay Edge is Chair of the Graduate Architecture Program at Virginia Tech. She oversaw the project along with Assistant Professor Edward Becker. Edge had been looking for a studio project of the right scale and complexity for her design students to build, and this was the perfect opportunity. The city commissioned Virginia Tech to build the tower with an emphasis on clean tech and low-carbon emissions and construction.
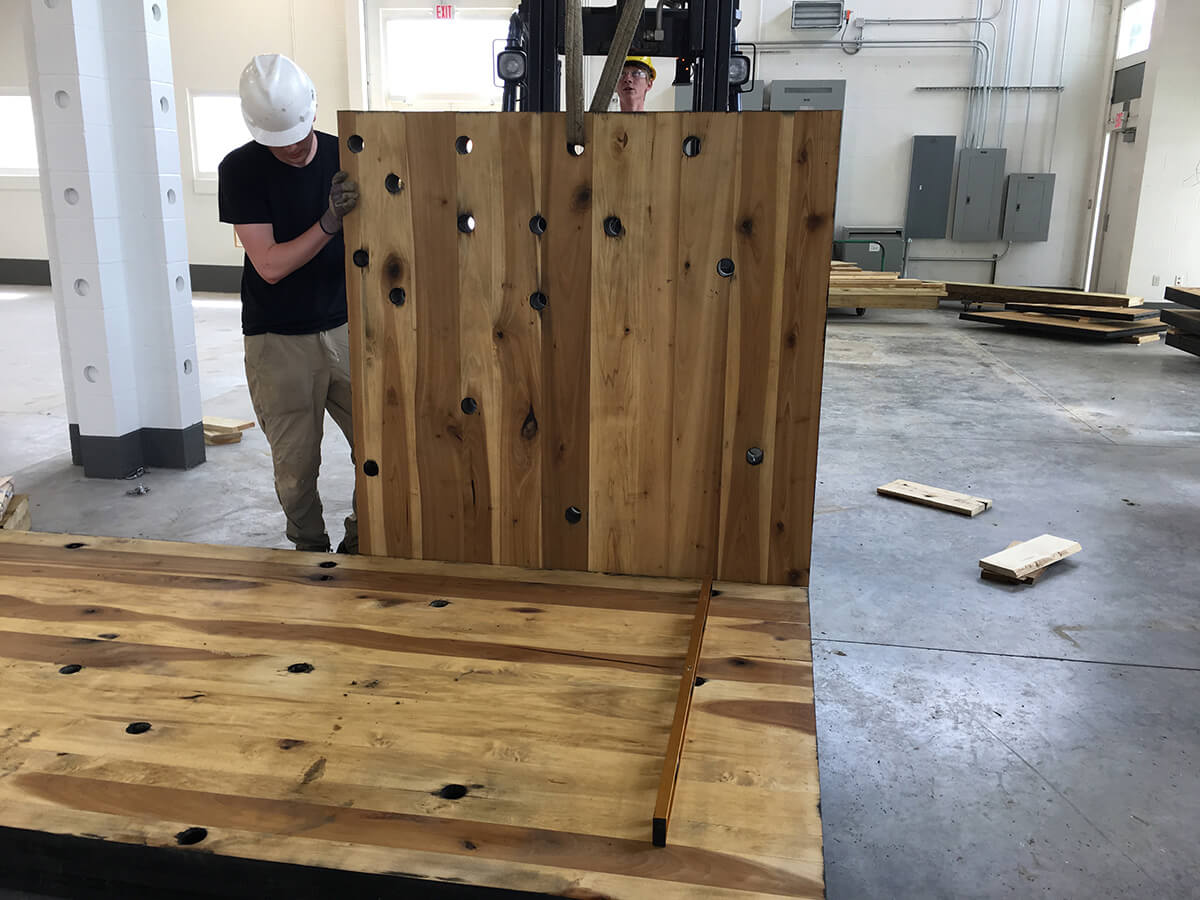
The New River Train Observation Tower project project started in the Spring Semester of 2018, and involved 12 Virginia Tech graduate students. The students toured the site, and were provided with 15 hardwood CLT panels measuring 5 ft x 10 ft—some were 3-ply and some were 5-ply. With guidance from professors Edge and Becker, they went through an iterative design and learning process. Completed in the Fall of 2019, the New River Train Observation Tower is believed to be the first permanent structure in the world to use prefabricated, hardwood CLT modules.
Initially, the plan was to use CLT (cross-laminated timber) for the tower. CLT is durable, aesthetically pleasing, and comparable to other building materials in sustainability. There were a couple of problems with this approach however. Industrially produced CLT panels would have to be shipped to location, (typically from Europe, Canada, or the Pacific Northwest) and the team determined that the carbon cost was too high.
The second problem was affordability. On top of the carbon cost, the shipping costs were prohibitive, and none of the manufacturers were willing to donate materials. To stay within budget, the team had to find another solution. Luckily, it was in their own backyard.
Responsible Local Sourcing
Professor Dan Hindman and other faculty in the Virginia Tech Department of Sustainable Bio-Materials had been research-testing yellow poplar CLT prior to the tower project. CLT is normally made out of softwood species, not hardwood, but yellow poplar is a plentiful local resource. Edge consulted with them, and they encouraged her to use the new product, which had several advantages. Obviously, using locally sourced wood would reduce the carbon footprint and shipping costs. Yellow poplar is also an abundant species that grows quickly and replenishes itself without cultivation. It was a cost-saving choice as well, as the wood was donated by local sawmills, and the panels were pressed, cut, and digitally altered by the Southern VA Higher Education Center, a nearby trade school.
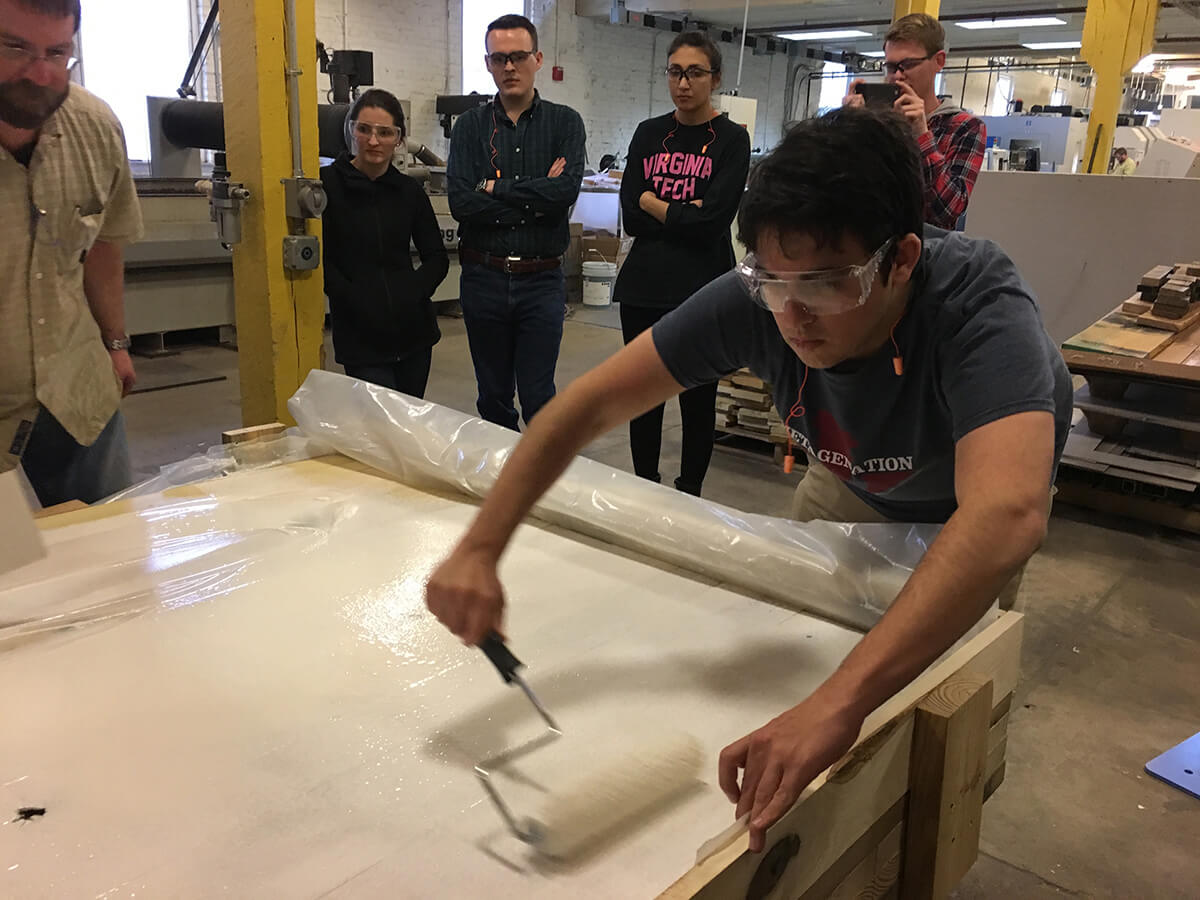
“The real-world experience they got from participating in this project was invaluable,” explained Associate Professor Kay Edge, chair of Virginia Tech's Graduate Architecture Program. “They saw the benefits of using locally sourced materials, and since part of the project was prefabricated at our research facility and part was site-built, they could see the ease and efficiency that is offered by offsite construction.”
Real World Experience
The tower project started in the Spring Semester of 2018, and involved 12 graduate students. The students toured the site, and were provided with 15 panels measuring 5 ft x 10 ft—some were 3-ply and some were 5-ply. With guidance from professors Edge and Becker, they went through an iterative design and learning process. The students were responsible for the design of the structure, as well as a considerable amount of the hands-on construction.
While most of the design took place on computers in the classroom, the students also met with the clients, city officials, building officials, engineers, and suppliers.
A structural engineer provided stamped drawings for city approval. The first question they got when they applied for permits was “Are the CLT panels ANSI rated?” They weren’t, but the permitting officials were satisfied by the research and data provided by the Sustainable Bio-Materials department, which showed that the hardwood CLT was actually stronger that the typical CLT product.
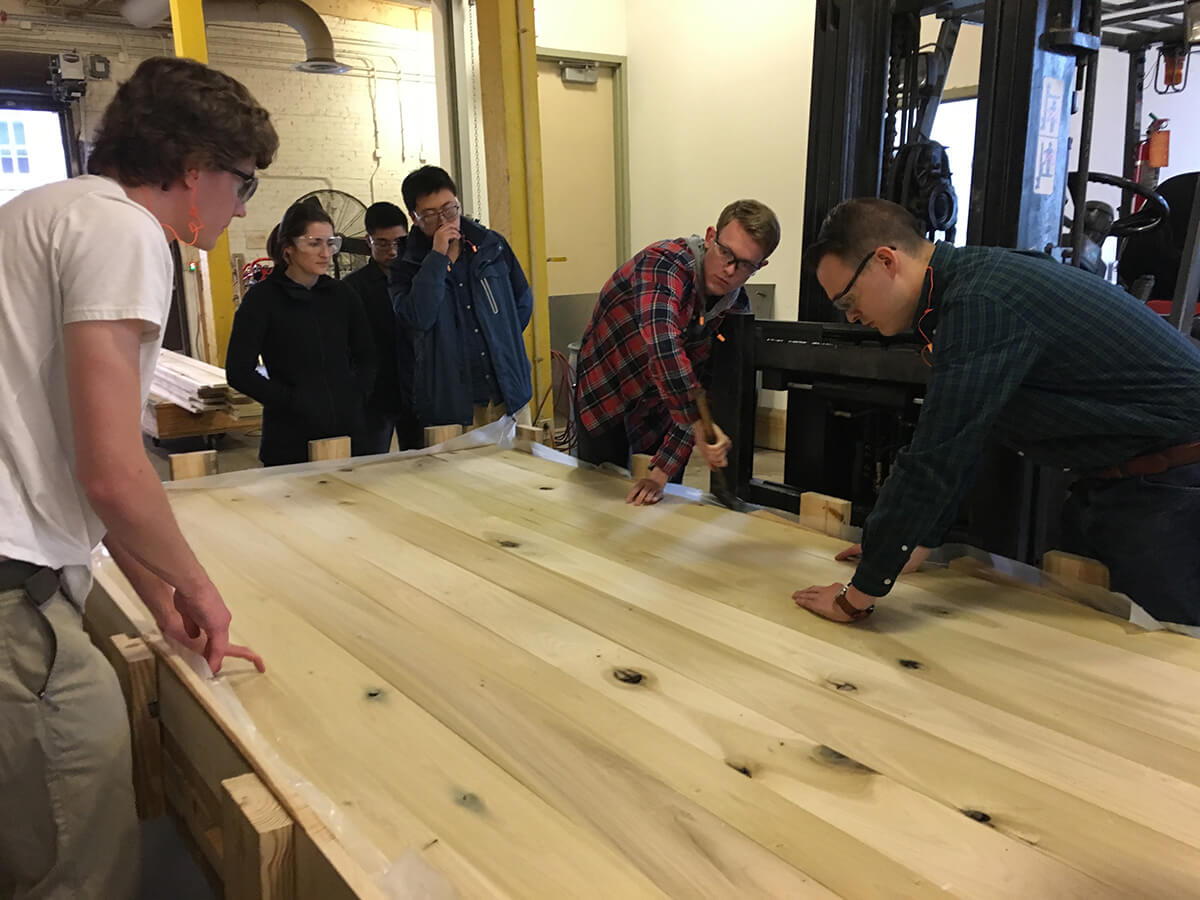
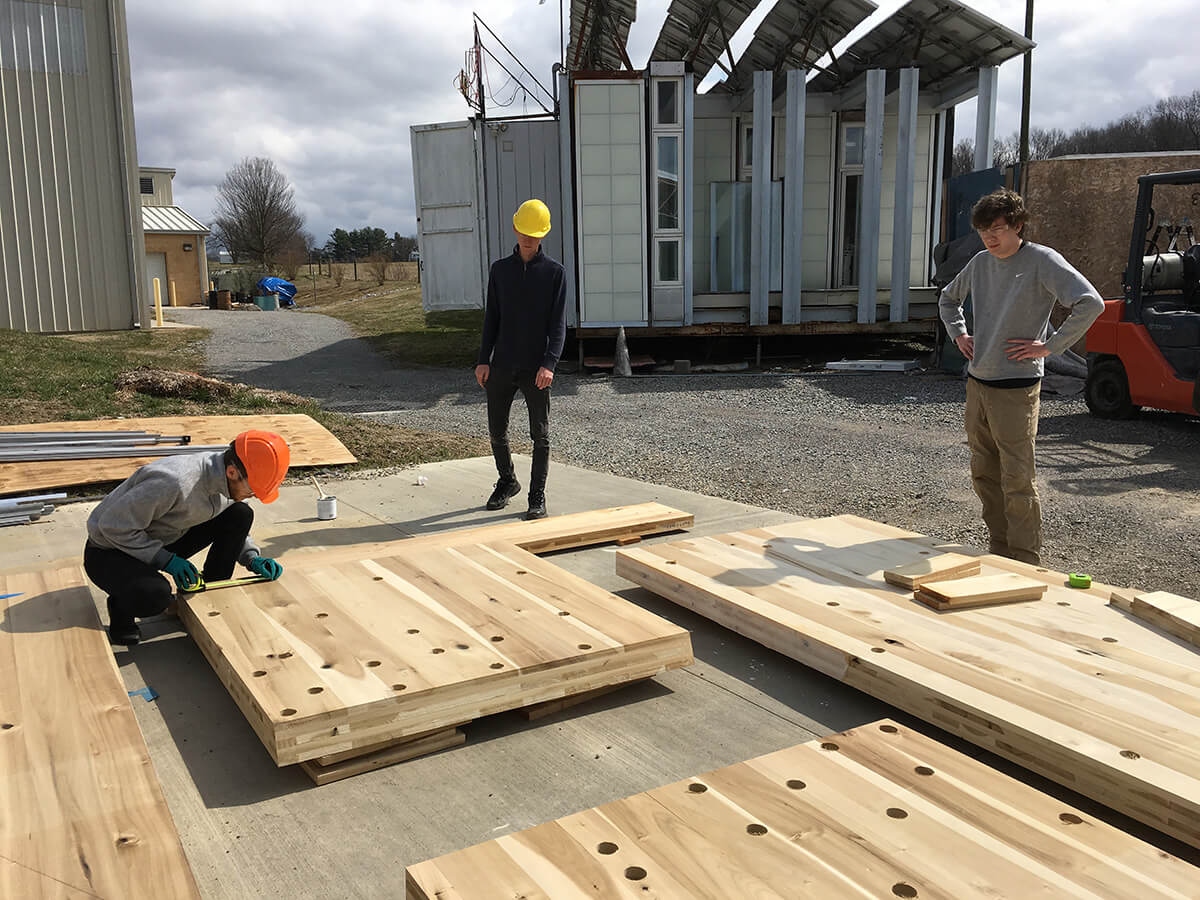
Thoughtful Design
The students incorporated thoughtful design throughout, from the handicap accessible walkway to the angle and position of the two modular viewing platforms. They also included functional but playful elements, including the dramatic angular design, and random holes in the panels for viewing, air flow, and a “dappled light” effect. They even tilted some of the steel supports to mimic the surrounding trees.
One of the modules was built by the students at the VT architecture research facility, where they had access to forklifts and other tools. The other module was built on-site by the students.
“The students spend so much time in front of the computer screen, that anytime you can get them in a real-world construction situation is great.” said Professor Edge. “There’s always the worry that they won’t understand the implications of what they are drawing. In this case, it really was driven home. There is so much precision you can get with a computer program, but that precision doesn’t exist on the job site.”
“They could also see the challenges involved,” she said. “In this case we had to figure out how to get the module that was built off-site onto a truck and to the site, and then get a crane in there to lift the prefabricated module into place.”
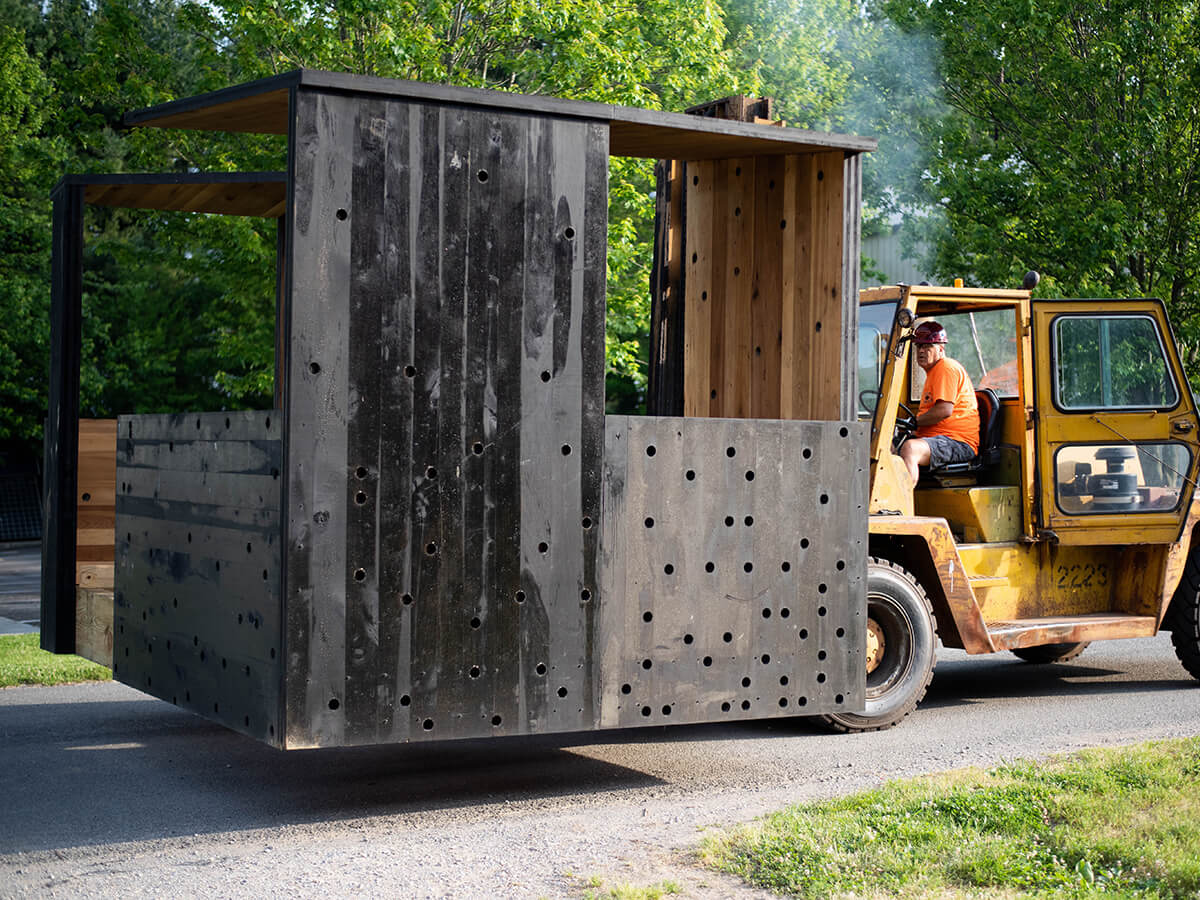
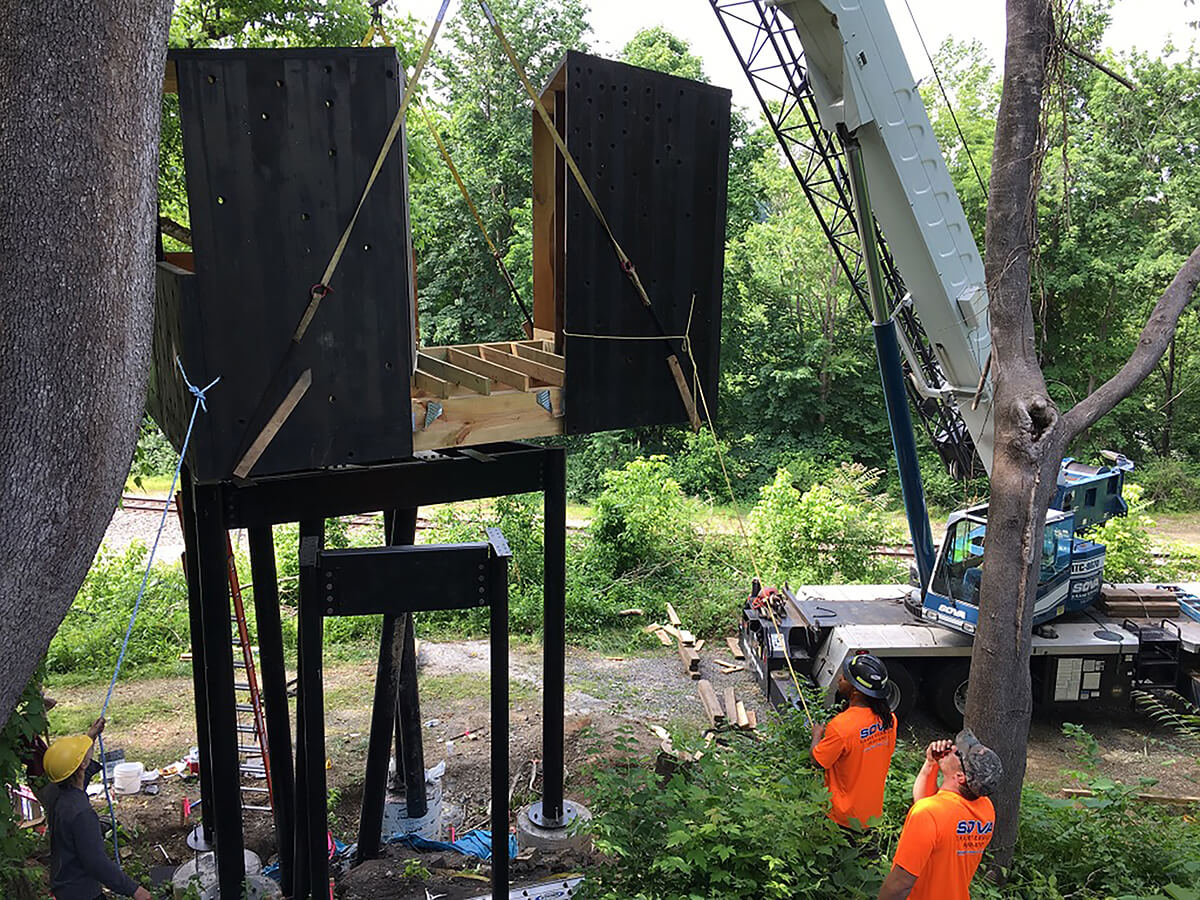
A Local Project with Global Impact
Local businesses stepped up to help the students keep costs down. The wood and the structural steel were donated, as were the helical piles used to anchor the foundation. The roofing membrane and the structural-rated glue used to adhere the layers were also donated.
The students gained practical, hands-on knowledge that simply can’t be taught in the classroom.
“The real-world experience they got from participating in this project was invaluable,” explained Edge. “They saw the benefits of using locally sourced materials, and since part of the project was prefabricated at our research facility and part was site-built, they could see the ease and efficiency that is offered by offsite construction.”
Completed in the Fall of 2019, the New River Train Observation Tower is believed to be the first permanent structure in the world to use prefabricated, hardwood CLT modules. The Virginia Tech Sustainable Bio-Materials Department is working on getting their HCLT product code-approved, which is a lengthy process. In the meantime, they are getting the word out. Outreach has included presentations to the American Hardwood Export Council and other professional organizations with an interest.
If you would like to learn more about this unique hardwood CLT product, contact Kay Edge (540) 231-1212 kedge@vt.edu or Edward Becker egb@vt.edu.
About the Author: Margie Schramke is a freelance writer and designer with a background in modular building. She spent three years as a local journalist and seven years as the Marketing Manager of a large modular construction company. You can contact her at margieschramke@gmail.com.
Don't Miss Our Upcoming Events!
Join the leading companies and professionals from across the offsite construction industry at each of this year's Offsite Construction Network events. With summits and expos taking place across North America in 2025, it's never been easier to connect with and learn from offsite construction manufacturers, designers, builders, and suppliers from the United States and Canada.
Subscribe today to get the latest updates on future events from the Offsite Construction Network.